Last Updated on July 15, 2025 by Packoi Team
In today’s competitive market, the right packaging shapes how customers perceive your product. Among many available options, rolled packaging stands out for its versatility, cost-effectiveness, and compatibility with automated machines.
In this blog, we’ll explore rolled packaging, how it works, and why it could be an excellent choice for your business. We’ll also walk through a step-by-step guide to help you choose the right rolled packaging tailored to your product needs.
Let’s dive in!
What is Rolled Packaging?
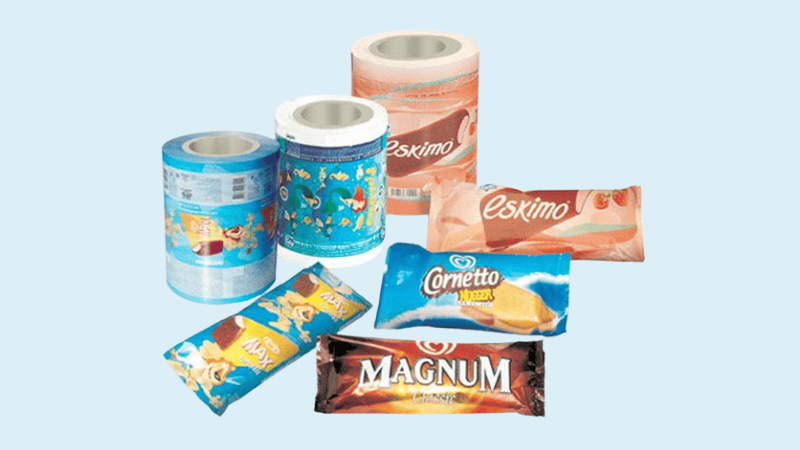
Rolled packaging is simply a type of flexible packaging that comes in the form of large rolls. These rolls are made up of a continuous sheet of flexible materials like plastic, film, paper, or foil, all wrapped around a cylindrical cardboard center piece called a core.
One of the biggest differences between rolled packaging and rigid packaging (like carton board, cardboard boxes, or hard plastic containers) is flexibility. Rigid packaging holds its shape and does not bend easily, while rolled packaging is bendable and easy to work with.
Rolled packaging is commonly used for products like snack packs, candy bars, coffee bars, and medical products. It’s especially popular among small businesses and online brands because it’s cost-effective, space-saving, and highly customizable.
How Flexible Packaging Rolls Work?
Flexible packaging rolls, also known as roll stock, are widely used for efficient, high-speed packaging across various industries. These rolls are specifically designed to be used with automated Form Fill Seal (FFS) machines that handle everything from shaping to sealing.
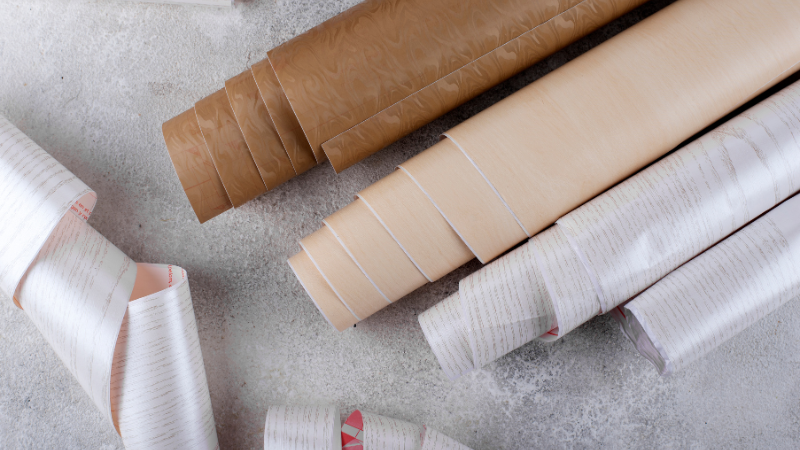
FFS machines can have a vertical or horizontal construction. Vertical FFS machines are ideal for snacks, grains, powders, and liquids. Horizontal machines, on the other hand, are better for solid or pre-shaped products like candy bars, medical supplies, and fragile items.
Here’s a simple step-by-step breakdown of how flexible roll stock is used:
Step 1. Loading the Roll
The process begins with mounting the roll of packaging material onto a spindle. This allows the material to unroll smoothly and feed into the machine, minimizing handling issues.
Step 2. Forming the Shape
The machine pulls the roll and folds the material into the desired packaging shape, typically bags, pouches, or wraps, depending on the product and film type.
Step 3. Filling the Product
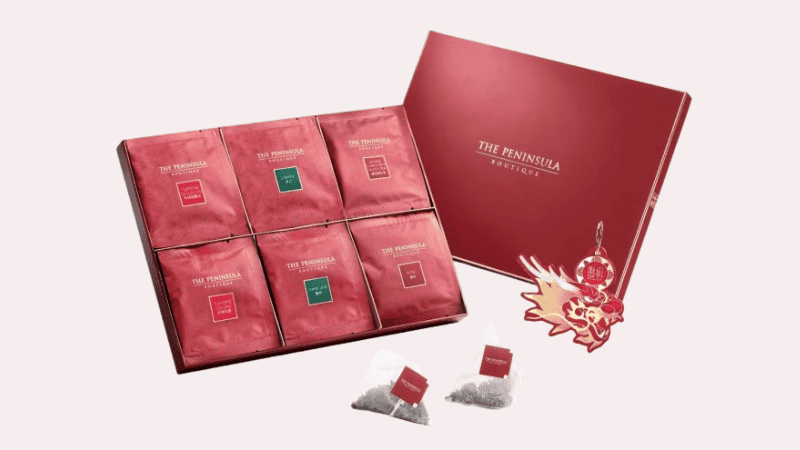
Once the material is shaped, the machine fills it with the actual product, such as snacks, powders, capsules, etc. Timers or sensors are often used to ensure the packaging is accurately filled and prevent issues like overflows or spills
Step 4. Sealing the Package
After filling, the machine seals the package by applying pressure or heat, depending on the material. Some materials have heat-resistant properties, making them suitable for products requiring thermal sealing.
Step 5. Printing and Labeling (Optional)
The flexible packaging rolls can be printed with branding details like logos and taglines. We can also add ingredients, barcodes, or legal info. This can be done before loading the roll or inline during the packaging process to meet other specifications.
Ready to Get Custom Packaging for Your Business?
start with a low minimum order quantity
5 Most Commonly Used Types of Rolled Packaging
Rolled packaging can be made from different materials, each offering its strengths, levels of protection, and visual appeal. In this section, we’ll explore the five most common types of roll-stock packaging materials available in the market:
1. Plastic Rolls
Plastic is one of the most commonly used materials in rolled packaging, and for good reason. Plastic rolls are lightweight, affordable, and adaptable across industries. Typically made from high-density polyethylene (PE), polypropylene (PP), or polyethylene terephthalate (PET), they can be easily converted into produce bags, stand-up pouches, bin liners, and wraps.
Besides affordability, another major advantage of plastic rolled packaging is its barrier properties. Its moisture resistance helps keep contents dry, making it ideal for frozen foods, dry snacks, personal care items, and sensitive products..
Plastic rolls are also easy to print on, which significantly benefits branding, labeling, and compliance in retail markets. Small businesses and high-volume brands often favor them for their versatility and cost-effectiveness. However, they may not be suitable for brands prioritizing sustainability and focusing on sustainable packaging.
2. Film Rolls
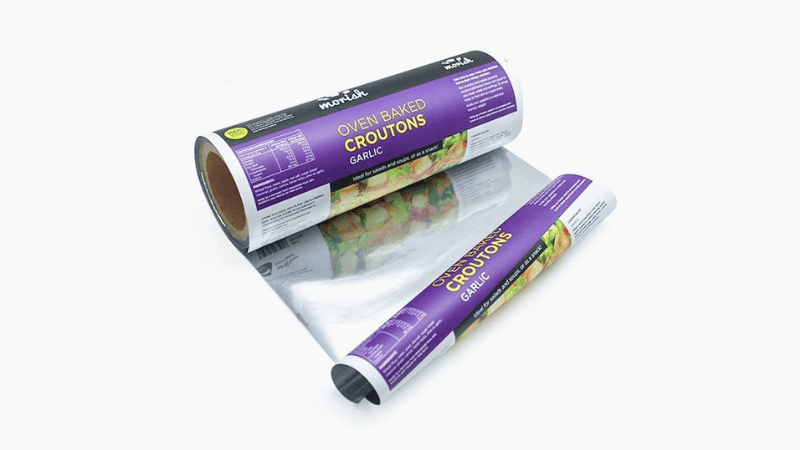
Film rolls are widely used in high-speed packaging applications. These can be made from single or multiple film layers, depending on the product’s barrier requirements. Common materials include PE, PP, biaxially oriented polypropylene (BOPP), and PET.
The flexible film rolls are considered one of the best solutions for packaging food products due to their ability to maintain freshness and provide a clean, glossy finish. They are commonly used for frozen food packaging, dry fruits, and candy wrappers.
A major advantage of packaging film rolls is their compatibility with various sealing methods and high-speed packaging machines, ensuring efficiency and product integrity. These can also be customized with high-resolution printing and eye-catching designs, making them a go-to choice for the food and pharmaceutical industries.
3. Paper Rolls
As businesses shift toward sustainable alternatives, paper-based roll packaging is gaining popularity. These rolls, typically made from kraft paper or coated papers, offer a functional and eco-friendly alternative to plastic.
Although paper rolls don’t offer strong natural barrier properties, they can be wax-coated or lined with bio-based films to make them resistant to water and grease. This makes them ideal for wrapping baked goods, sandwiches, pet food, and dry groceries. They’re also frequently used in secondary packaging, such as wraps or inner liners.
Some of the main benefits of paper roll packaging include being sustainable and recyclable when uncoated, having a natural aesthetic appeal, and the availability of multiple custom printing options. There are various types available based on weight, thickness, and coating, each serving specific product needs.
4. Aluminium and Metallized Film Rolls
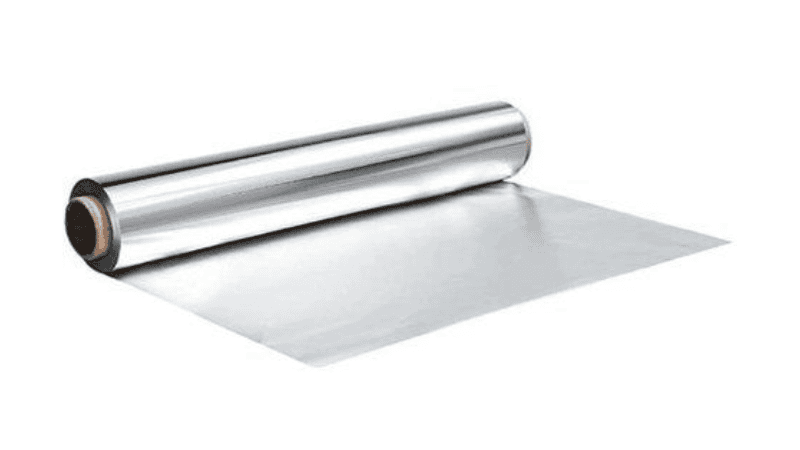
Foil and metalized rolls are the gold standard for high-barrier protection. Aluminum foils are made up of real sheets of aluminum, while Metallized films are basically plastic films like PET coated with a layer of aluminum to give off a metallic finish with better flexibility than real aluminum foil.
Both types of packaging protect against light, oxygen, and moisture, so the product can have a long shelf life. Such foils are popular in pharmaceuticals, coffee and tea packaging, and high-fat foods like chocolates and cheese.
Apart from excellent barrier properties, another major advantage of aluminum and metallized film rolls is that they appear premium and improve product visibility and consumer perception because of their reflective finishes. The only downside of these rolls is that they are harder to recycle unless paired with some specialized systems.
5. Laminated or Multi-Layer Rolls
Rounding up the list, we’ve got laminated or multi-layer rolls. These rolls are made by combining two or more materials into a single structure to get the best features of each layer. Common structures in multi-layer rolls include:
- PET and PE
- Paper and PE
- PET, Aluminium, and PE
PET offers printability and toughness, while PE provides the benefits of heat-sealing and moisture resistance. Paper is used for aesthetics, and aluminum provides excellent barrier properties.
These rolls are perfect for packaging fragile items or products requiring puncture resistance, such as sauces, oils, medical kits, or pet food. The durability of laminated structures makes them ideal for handling heavier loads while maintaining seal integrity.
Ready to Get Custom Packaging for Your Business?
start with a low minimum order quantity
Stepwise Guide On Choosing the Perfect Roll Packaging for Your Business
Choosing the right roll packaging means aligning your packaging solution with your product needs, business goals, and operational capabilities. This step-by-step guide will walk you through selecting the best roll packaging and sourcing it from a reliable supplier.
1. Evaluate Your Product Type and Storage Needs

Start by understanding your product type and how it will be stored. Different products require different levels of protection and flexibility. For example, frozen food packaging needs to be moisture resistant, while dry snacks require packaging that preserves freshness.
2. Determine Shelf Life and Barrier Requirements
Product shelf life is critical. Exposure to oxygen, moisture, or light can degrade your product and impact quality. Choose materials with the right barrier properties to extend shelf life and reduce waste.
3. Ensure Compatibility with Packaging Equipment
Consider the compatibility of the rolling with your existing packaging equipment and test the material on your line. Most modern packaging lines use FFS equipment, and if your material doesn’t feed, seal, or cut properly, you risk downtime, unnecessary costs, and product waste.
4. Balance Budget with Sustainability Goals
Cost matters, but so do brand values. If sustainability is important to your brand, you must make the right budget-sustainability trade-off and opt for environmentally friendly and recyclable materials. For instance, plastic rolls are often the most affordable solution, but they may not align with your sustainability goals.
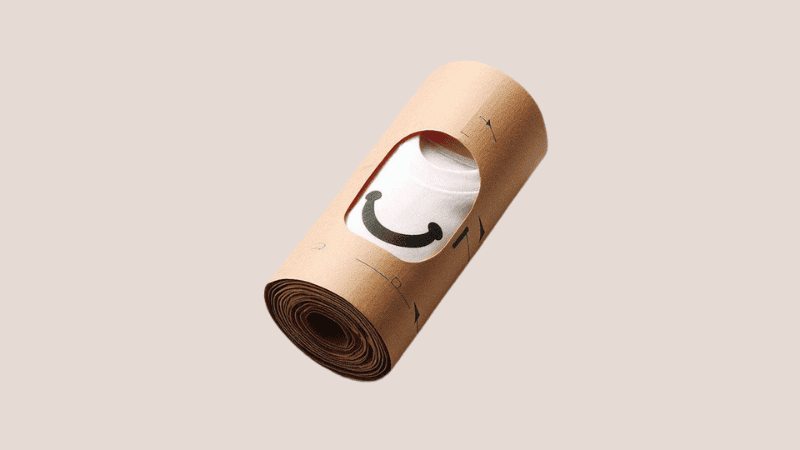
Paper, compostable films, and recyclable laminates offer eco-friendly packaging but can be more expensive. Make the right choice considering your budget and brand values.
5. Research and Select a Reliable Supplier
Find a supplier with quality certifications, strong reviews, and a positive customer satisfaction rate. Request client references and inquire about their after-sales support. Look for wholesale suppliers that offer high-quality materials and customization options.
6. Ask Smart Questions Before Ordering
Before placing your first order, clarify important details like:
- What is the lead time?
- What is the minimum order quantity?
- Are the materials FDA (Food and Drug Administration) or EU compliant?
- Does the supplier offer custom printing and sizing?
- Can I get samples?
7. Finalize Customization
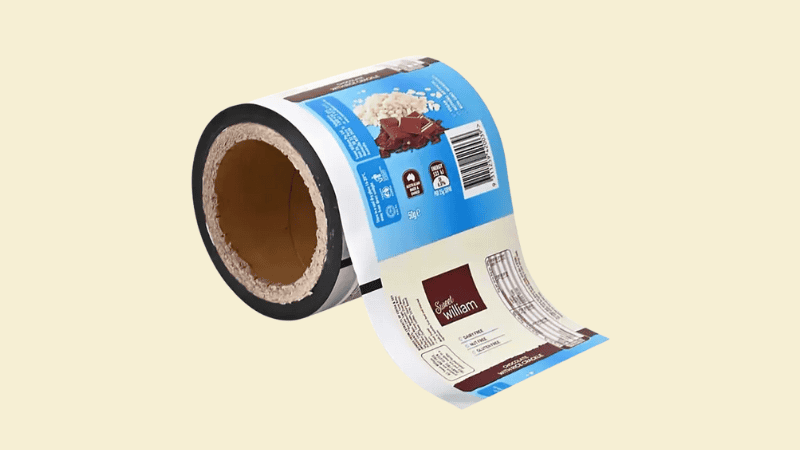
Once you’ve selected a supplier and material, it’s time to customize the packaging to match your brand and product needs. Provide all the important details, including roll width, core diameter, thickness, sealing requirements, and design preferences.
For custom printing, you need to confirm details such as color accuracy, finish, and positioning of logos, ingredients, and barcodes. Double-check all details to ensure a durable and efficient packaging system.
Key Benefits of Using Rolled Packaging
Rolled packaging has become the go-to solution for brands seeking efficiency, scalability, and flexibility. Here are the core advantages that make it a smart choice for modern businesses:
Storage and Shipping Efficiency
One of the biggest advantages of roll stock is its compactness. It occupies less space than pre-formed packaging, making it easy to store and more cost-effective to transport. This is especially useful for businesses operating at scale or managing inventory across multiple facilities.
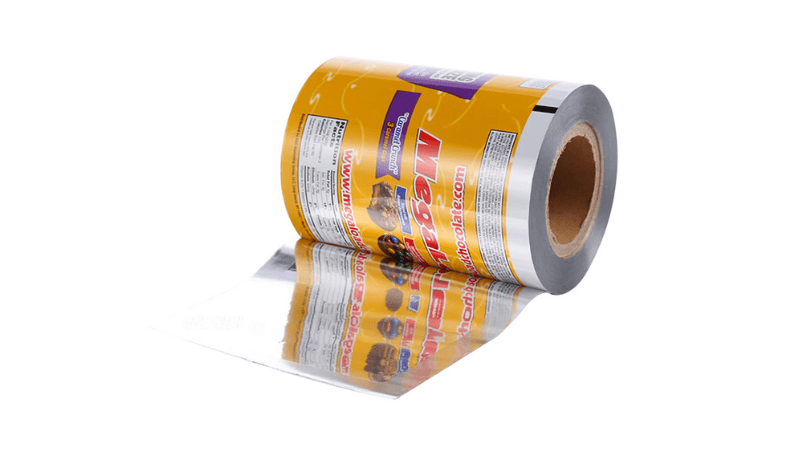
Less Waste, More Product
Rolled packaging uses only as much material as needed, which means minimal excess and less packaging waste per unit. It also improves the product-to-packaging ratio, maximizing efficiency and reducing environmental impact.
Customization Options
From structure and thickness to finishes and print design, rolled packaging offers excellent customization. You can add features like resealable zippers, matte or gloss coatings, and barrier layers depending on your product requirements.
Cost Advantages for Scaling
Roll stock offers big financial advantages for businesses looking to scale, as it’s lightweight, compact, and efficient to produce. As production volume increases, the cost per unit drops, boosting your overall margins.
Works with Automated Packaging Equipment
Roll stock packaging is made for automation. It runs smoothly on FFS machines and other automated systems, which is ideal for high-speed production environments. This also minimizes human intervention, reduces packaging costs in the long run, and supports consistent product sealing.
Applications of Rolled Packaging across Industries
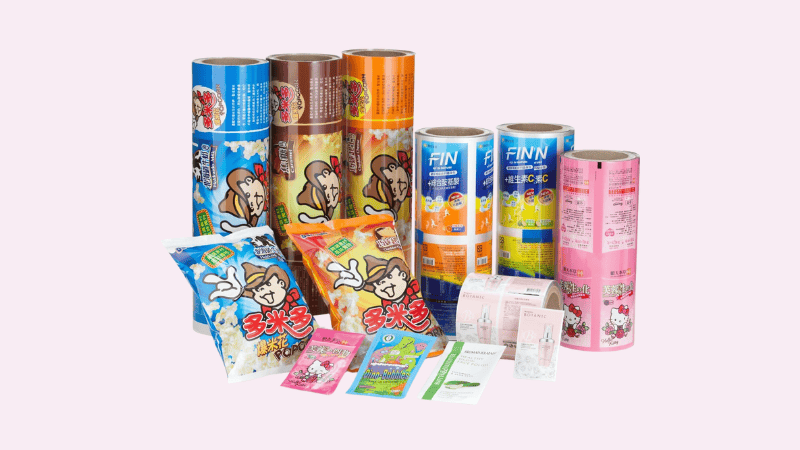
Rolled packaging is a flexible packaging solution that has found its way into a wide range of industries, including food, e-commerce, healthcare, and beauty. Let’s take a quick peek at some of the important sectors where rolled packaging is used:
Food and Beverage
Food and beverage is the industry where rolled packaging truly excels. From chips and frozen vegetables to sauces and dry snacks, rolled packaging keeps products safe and fresh. Also, since food packaging usually needs to move quickly on high-speed machines, roll stock’s compatibility with automated systems makes it a valuable choice.
Retail and E-commerce
For retail and e-commerce brands, roll stock packaging offers a practical way of bundling, sealing, and protecting products. It creates custom pouches for apparel, cosmetics, accessories, and even small electronics.
Healthcare
Rolled packaging is often chosen for medicine sachets, diagnostic kits, and surgical gloves, as it can be customized for safety and compliance. Another reason for its popularity in the healthcare industry is its reliable seal integrity and compatibility with batch tracking and labeling needs.
Beauty and Personal Care
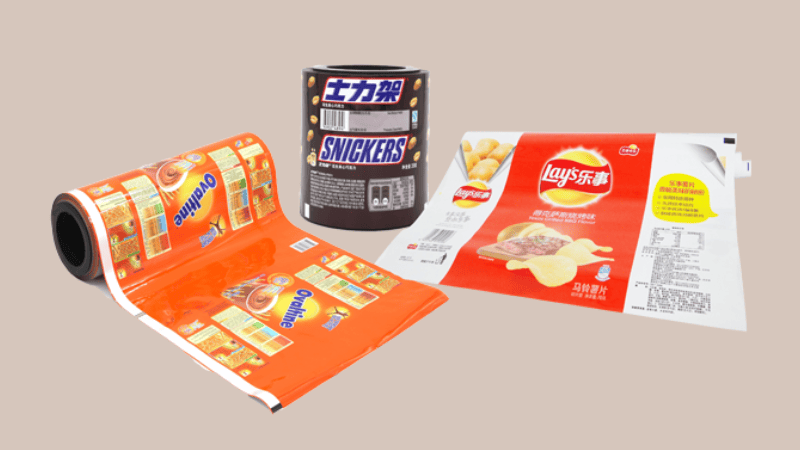
Rolled packaging is also widely used for beauty and personal care products. It is ideal for packing face masks, serums, and travel-size shampoo kits. It allows easy portioning, protection, and attractive presentation.
Pet Food and Supplies
From small treat pouches to larger pet food bags, rolled packaging plays a big role in the pet care industry. Brands can offer resealable closures, transparent windows, or easy-open features for pet owners.
FAQs
What is the first step in choosing the right rolled packaging for a business?
The first step is to evaluate your product type and storage needs to determine the necessary level of protection and flexibility for the packaging.
What are the key benefits of using rolled packaging for businesses?
Key benefits include storage and shipping efficiency, less material waste, extensive customization options, cost advantages for scaling, and seamless compatibility with automated packaging equipment.
What is the main advantage of aluminum and metallized film rolls?
Their main advantage is providing high-barrier protection against light, oxygen, and moisture, extending product shelf life for sensitive items.
Conclusion
In this comprehensive guide, we discussed rolled packaging and its common types and listed its advantages and applications. We also explored how to choose the right roll stock for your product while keeping the costs low and maximizing efficiency.
Now that you understand how rolled packaging can support your brand and scale your operations, you’re ready to take the next step toward your first custom roll stock packaging solution.
Get Your Dream Custom Rolled Packaging with Packoi
With over 25 years of industry experience and a global client base, Packoi is your trusted partner for premium custom packaging and printing solutions. What sets us apart? Certified quality materials, sustainable options, competitive pricing, and exceptional customer support.
At Packoi, we offer a wide range of custom boxes, bags, and marketing materials, all meticulously designed to match your brand’s unique identity. To get a free quote, contact us today!