Last Updated on February 25, 2025 by Packoi Team
Polyethylene-coated paper is a crucial material used in a wide range of food packaging applications. Notably, food packaging plays a significant role in guaranteeing the safety and quality of packaged products.
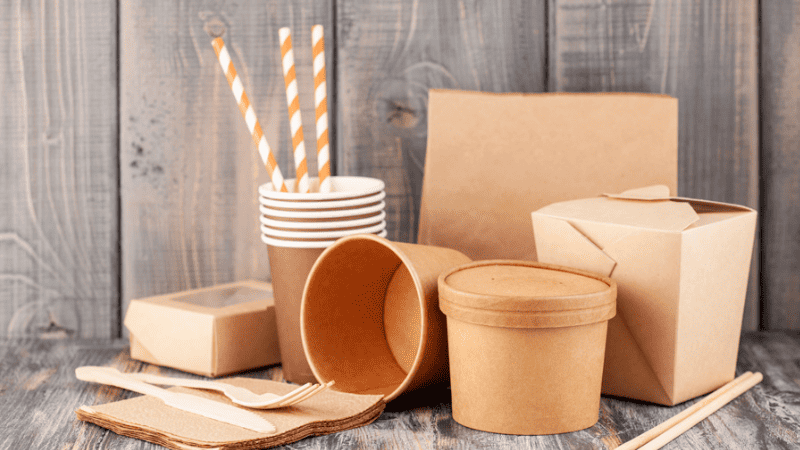
Therefore, this paper type is used as one of the paper packaging materials due to its ability to protect contents from moisture, grease, and other contaminants. It is an ideal choice for packaging items like food products, including baked goods, fast food, frozen food, and snacks.
This blog article aims to delve deeper into the science behind making the paper, starting with its composition. We will explore the different types of PE coatings used in paper manufacturing, their properties, and how they contribute to the material’s overall performance.
It is also crucial to understand the paper production process, including the equipment and techniques used to apply the coating to the paper.
Furthermore, the article examines the benefits and limitations of using this paper type in food packaging, including its impact on food safety, shelf life, and consumer convenience. Another aspect that will be highlighted in the discussion is the environmental implications of using the paper, considering if it is recyclable and biodegradable.
What Is PE-Coated Paper?
The paper type has a polyethylene (PE) coating layer on one or both sides, applied to the paper using an extrusion coating. In the process, a molten layer of PE is extruded onto the paper surface and then cooled to form a solid, uniform coating.
Composition of the Paper
The composition of the PE coating can vary depending on the intended purpose or use.
- The specific properties required also influence the composition of the paper.
- PE paper coatings utilize low-density polyethylene (LDPE). This thermoplastic material is resistant to moisture, grease, and other contaminants.
- The thickness of the paper coatings varies depending on the purpose, ranging from a few microns to several hundred microns.
Properties of the Paper
The properties of the paper make it an ideal material for food packaging.
- The PE coating protects against moisture, grease, and other contaminants. Due to its ability to protect is mostly applied in food packaging to avoid compromising its safety and quality.
- The paper is also heat sealable, creating a secure, airtight seal that preserves the freshness and quality of the contents.
- The paper is also printable. Its smooth and uniform surface makes it suitable for high-quality graphics, logos, and text printing. Therefore, it is an excellent food packaging choice requiring branding and labeling.
Overall, the composition and properties make it versatile for food packaging, providing protection, freshness, and branding opportunities.
Ready to Get Custom Packaging for Your Business?
start with a low minimum order quantity
6 Types of PE-Coated Paper
The paper comes in various types and forms with different compositions, thicknesses, and properties. Below, we dive into detail, discussing the different types of paper coatings.
1. Single-Side PE-Coated Paper
This type of paper has a layer of PE coating on one side of the paper, making it water-resistant and suitable for applications where one side needs to be protected from moisture. The single-side coated type is commonly used as food packaging for snacks, baked goods, and fast food.
2. Double-Side PE-Coated Paper
As the name suggests, this type of paper is coated with PE on both sides, making it water-resistant and grease-resistant. The double-sided option is used for packaging frozen food, meat, and seafood.
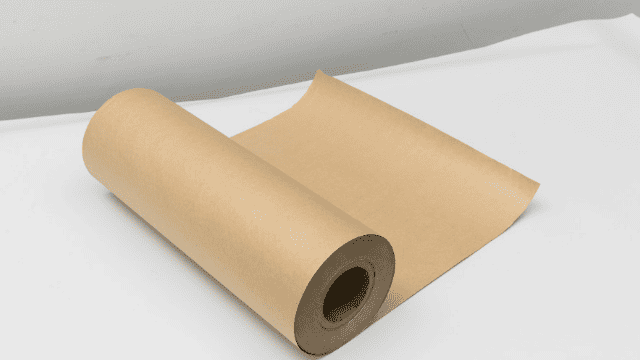
3. Sandwich PE-Coated Paper
This type of paper has a layer of PE coating between two layers of paper, making it highly water-resistant and suitable for applications where both sides need to be protected from moisture. The sandwich-coated option is used as food packaging, especially for sandwiches, burgers, and other fast food items.
4. Release Liner PE-Coated Paper
This paper is a release liner for pressure-sensitive adhesives, such as labels and tapes. The coating offers barrier properties to prevent the adhesive from sticking to the paper surface.
5. Matte PE-Coated Paper
Matte Pe-coated paper has a dull, non-reflective surface, providing a natural, muted look. The paper is used for printing high-quality graphics, where a non-glossy finish is desired, like images and logos.
6. Glossy PE-Coated Paper
Glossy PE-coated paper has a shiny, reflective surface that enhances the colors and contrasts of printed graphics. The glossy-coated option is used for printing high-quality graphics, like product labels and marketing materials. It is ideal when a glossy finish is desired on the final product.
The different types of polyethylene paper options offer specific features and benefits that make them suitable for various applications. The most popular applications are in the food packaging and labeling industries. The choice of the type of paper depends on the needs, such as moisture resistance, printability, and aesthetic appeal.
What Are the Benefits of Using PE-Coated Paper?
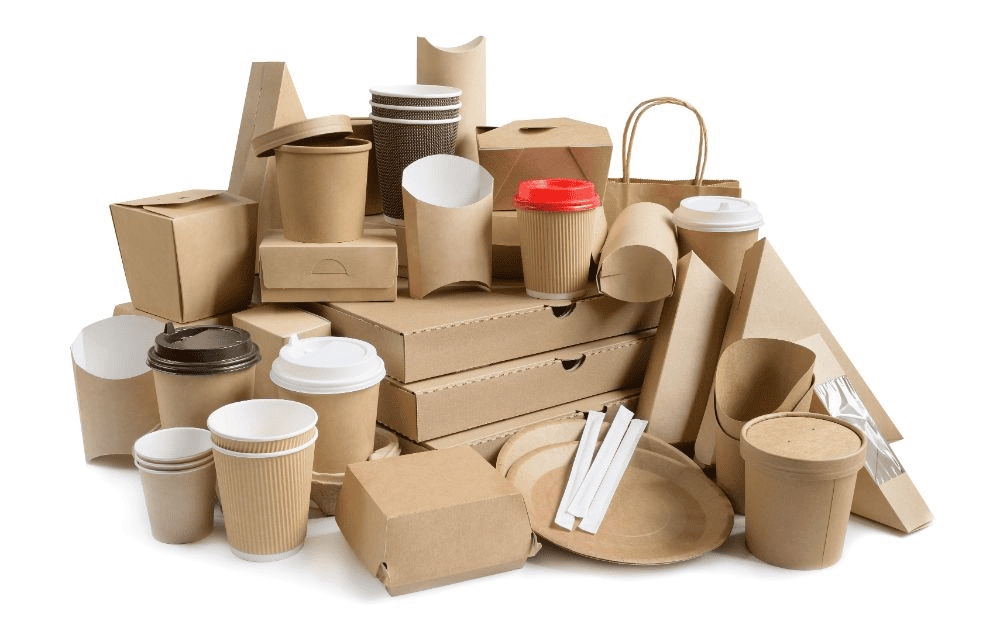
Paper coated with polyethylene has become a popular food packaging and labeling choice. The main cause of its rise in use and popularity is that it offers several benefits over uncoated paper-based materials. Here are some of the key advantages of using this paper as one of the packaging materials or printing paper.
1. Good Water Resistance
The PE coating provides an effective barrier against moisture, preventing the paper from becoming soggy and weak. This makes it ideal for packaging food items that require protection from moisture, such as baked goods, snacks, and frozen food.
The coating thickness varies depending on what is the intended use. The ability to resist water makes it one of the best food packaging papers available in the market.
2. Good Grease Oil Resistance
The polymer coatings act as barrier materials against oil and grease. The grease barrier properties prevent staining and contamination of food. Also, this property makes it ideal for packaging greasy or oily foods, such as fried foods and fast food.
If you are looking for packaging materials in your fast food restaurant, settling for polymer paper is effective compared to uncoated paper options.
3. Good Heat-Seal Ability
The paper coated with the polymer can be heat-sealed, providing a secure and airtight seal that helps preserve the food’s freshness and flavor. Heat sealing also provides tamper-evident packaging, guaranteeing the safety and quality of the food. This property makes papers coated with excellent polymer barrier materials against tampering.
4. Relative Chemical Inertness
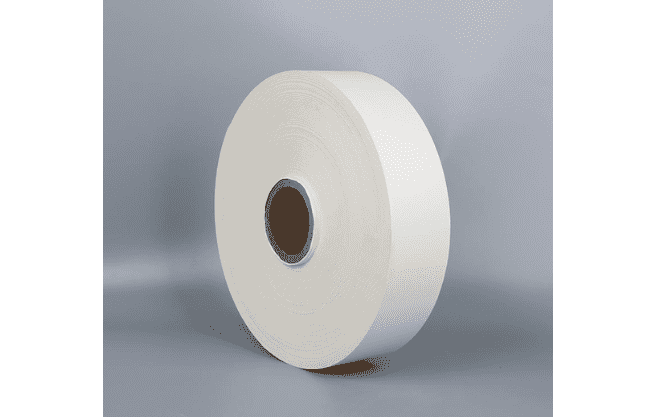
The PE coating is relatively chemically inert, implying that it does not react with the food or other substances it comes into contact with. This makes it a safe and reliable material for food packaging and labeling. Polymer-coated paper options have excellent barrier properties against chemical reactions from food.
Depending on the coating thickness, you can always be sure that your food will not be contaminated when you use this paper type. The coating layer varies in size depending on the goal or purpose. Still, whether you use a thin or thick layer, PE-coated paperboard is an excellent option from the paper packaging materials available.
5. Flexible
The paper is flexible and easy to handle, making it a convenient and practical food packaging and labeling choice. Unlike plastic materials, this paper is effective when looking for reliable packaging materials in the food industry. You can always order your packages’ coated and uncoated paper samples and see which of the two is effective.
The coated paper samples come with flexible barrier materials against moisture, grease, and tampering. Even with a thin coating thickness, you can still get the best results with your polymer paper packaging.
6. Branding and Printability
The paper’s smooth surface provides a high-quality print surface for branding and marketing. This allows food manufacturers to create custom packaging, differentiating their products from competitors. Unlike plastic coatings, the polymer paper type makes quality branding for food companies.
The manufacturing process can produce quality printing papers for flyers, custom packaging, and other materials. Related closely to branding is the printability of the paper. The smooth and uniform surface of the paper makes it suitable for high-quality graphics, text, and logo printing.
The glossy outlook makes products packaged with this paper as a packaging material look appealing. The benefits of using the coating later on the paper are many and diverse. For the food industry, papers coated with polymers are among the best packaging materials available.
As a packaging material, the paper offers barrier coatings against water vapor transmission, grease, oils, and other contaminants. Polymer papers have strong barrier properties compared to uncoated paper packaging materials.
The coating layers make this paper type have good water and grease resistance, heat sealability, chemical inertness, flexibility, branding and printability opportunities, and tamper-evident packaging. These advantages make paper coated with polymer a versatile and reliable material for the food industry.
Ready to Get Custom Packaging for Your Business?
start with a low minimum order quantity
What Are the Disadvantages of PE-Coated Papers
The papers coated with polymer have several disadvantages, including:
1. Limited Barrier Properties
While polymer coating offers some level of protection against moisture, water, and grease, it lacks effective oxygen barrier properties and other gases. This makes it unsuitable for packaging applications that require high-barrier properties.
When packaged products require a low oxygen transmission rate, the polymer paper does not work effectively. Therefore, it is recommended that food items requiring low oxygen transmission rates use alternative packaging materials that provide strong oxygen barrier properties.
2. Poor Odor Barrier
The papers are not very effective at blocking odors. Although they have great grease barrier properties, they can’t prevent odors from entering the packages.
This can be a problem for applications where the odor of the packaged product needs to be preserved or prevented from affecting other products. This property is not ideal in food packaging applications because it can negatively impact quality and safety.
3. Recycling Requires Hydro Pulping
Recycling PE-coated paperboard requires hydroponics, a process that separates the paper fibers from the polymer coating using water and chemicals. The process is expensive and has limited recycling capabilities compared to other paper products.
The plastic waste generated from the recycling process also affects the environment. In food packaging applications, it is vital to use biopolymer-coated papers if you want to have a minimal environmental impact on your business.
4. PE-Coacted Paperboard Is Not Biodegradable
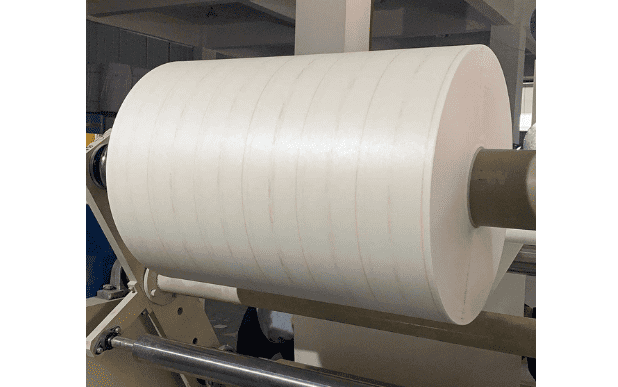
PE is a type of plastic that is not readily biodegradable. It can persist in the environment for hundreds of years, causing pollution and environmental damage. While some PE-coated papers may be compostable under specific conditions, they are not truly biodegradable.
However, biodegradable polymers can be used to design paper-based packaging. Biopolymer-coated paper packaging can reduce environmental impact and produce sustainable packaging for businesses.
5. Difficulty in Printing and Labeling
PE coating can make it difficult to print or label on the surface of the paper. If you want to use this paper type for printing projects, the surface must be treated with special coatings or inks to ensure adhesion and clarity.
However, PE-coated paperboard types are specifically designed for printing purposes. Therefore, make sure that you follow the standard test method to establish the right composition and properties to utilize during the extrusion coating process.
6. Higher Cost
PE-coated paperboard is generally more expensive than uncoated paper, which makes it less attractive for cost-sensitive applications. However, it is still the best option for preserving food quality and guaranteeing safety. Despite the high cost, coated paper samples have strong mechanical properties to guarantee paper resistance to wear and tear.
7. Limited Heat Resistance
PE-coated paperboard has a low melting point, making it unsuitable for high-temperature applications. The coating can melt or degrade, compromising the integrity of the packaging and potentially contaminating the product.
Ready to Get Custom Packaging for Your Business?
start with a low minimum order quantity
Therefore, depending on the application intended, the coating layer must be designed to resist extreme heat. There are numerous coating techniques applied that must suit the paper properties required for a specific purpose. The goal is to prevent damage from extreme heat and increase the product’s shelf life.
8. Environmental Concerns
The production of PE coating requires the use of fossil fuels, which contribute to greenhouse gas emissions and climate change. Additionally, the disposal of the papers can lead to environmental pollution and harm to wildlife.
Therefore, with regard to environmental issues, uncoated paper sample options are preferred over polymer papers. PE-coated paperboard has many advantages but produces negative impacts on the environment. This is because it is hard to recycle and not readily biodegradable.
13 Industries and Applications of PE-Coated Paper
There are several industrial applications where papers coated with polymers are used. Some of the common ones include:
1. Food Packaging
Papers coated with polymers are commonly used in the food packaging industry, particularly for applications that require moisture and grease resistance. This includes paper cups, paper salad bowls, paper soup cups, paper lids, and disposable food boxes and bags.
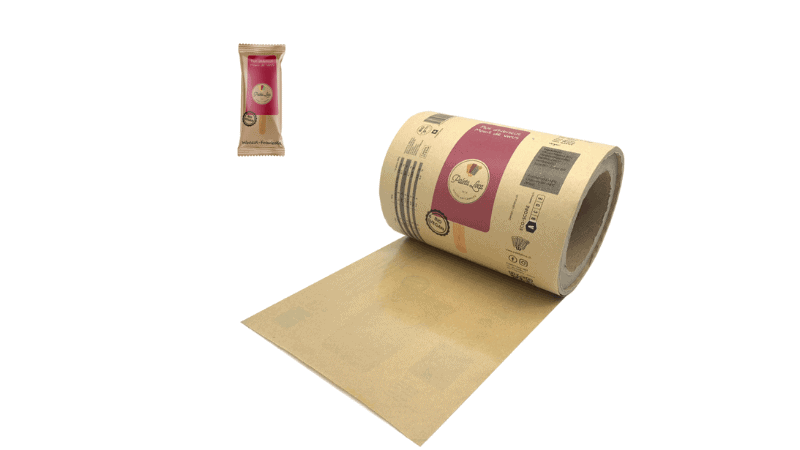
2. Medical Packaging
Papers coated with polymers can also be used for medical packaging applications, such as for medical devices, surgical supplies, and pharmaceutical products. The mechanical properties of the coating layer make it effective and reduce the water vapor transmission rate that can damage medical equipment and products.
The PE-coated paperboard effectively offers plastic coating resistance against contaminants when packaging drugs.
3. Labels and Stickers
Papers coated with polymers are also used for producing high-quality labels and stickers. These papers can be coated with a matte or glossy finish, depending on the application. With a low water vapor transmission rate, the labels and stickers have appropriate barrier coatings against vapors and other materials.
4. Coated Papers for Printing
PE-coated paperboard can be used for printing applications where a high-quality, glossy finish is desired. However, the physical properties of the printing paper must be determined earlier to ensure that the manufacturing process adheres to the specific needs. These papers are commonly used for printing brochures, magazines, and other promotional materials.
5. Specialty Papers
Papers coated with polymers are used to make or design specialty papers, such as those used for water-resistant maps, construction plans, and outdoor signage. They are also used to design printing papers for magazines, flyers, and other types of promotional materials. If you need special paper-based packaging, you can use PE-coated paperboard to design it.
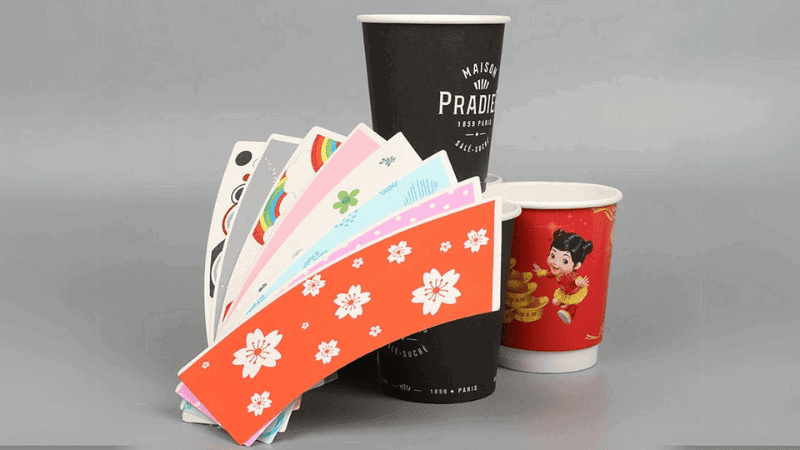
6. Wrapping Paper
Papers coated with polymers are used to produce wrapping paper resistant to moisture and other environmental factors. You can always test different polymer paper samples to see which one is the best fit for your business. The paper’s resistance against water vapor molecules should suit your standard packaging needs.
7. Textiles
Papers coated with polymers can also produce textiles, such as clothing and other wearable items. The paper resistance gives the coated paperboard excellent qualities for designing textiles for industrial use.
8. Gift Wrapping
Polymer-based papers are used for gift wrapping and packaging. The packaging industry has greatly benefited from using these paper types as gift wrappers. The material properties provide excellent aesthetic appeal for special gifts and packages.
9. Wallpaper
Polymer-coated papers are used as wallpapers, providing a durable and washable surface. Whether you want to decorate an office using branded materials, this is a go-to option because it has a high surface homogeneity that can make walls look appealing. The material properties and mechanical properties also make it washable, smooth, and glossy.
10. Bookbinding
Polymer-coated paper is used in bookbinding to provide a smooth and glossy surface. If you want to choose the right material for your books, you can also sample coated papers of different thicknesses. You can also consider biodegradable polymers to ensure that your bookbinding projects are sustainable.
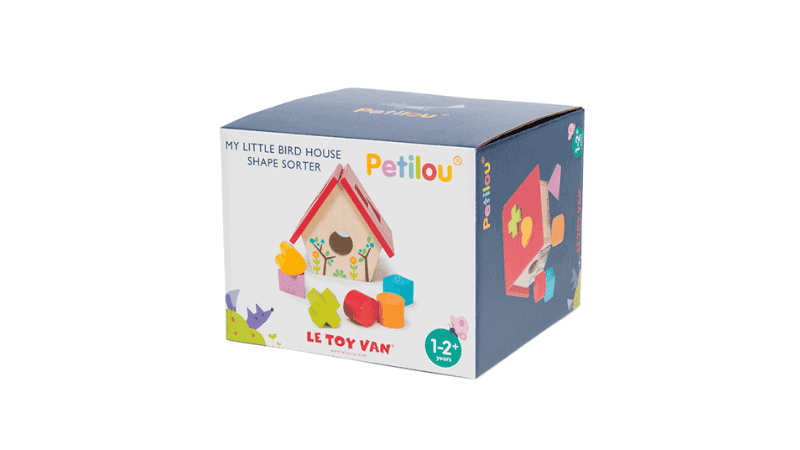
11. Art and Craft
Polymer-coated papers are used in various art and craft applications, such as scrapbooking, origami, and paper folding. With low-density polyethylene, you can design perfect arts and crafts that can be used as decorations in the home or office.
12. Retail Packaging
Polymer-coated papers are also used for retail packaging of various products, such as cosmetics, toys, and electronics. With this paper, you can make perfect contact angle measurements for products that require packaging in specific shapes.
For toys and electronics, you can create boxes with contact angle measurements that perfectly fit the products and prevent damage while in transit.
13. Disposable Tableware
Polymer-coated papers are also used in making disposable tableware, such as plates, bowls, and cups. With the strong mechanical properties of this paper type, you can produce strong disposable tableware for specific occasions.
The tableware designed from this material has strong barrier coatings against water, oil, and fluids. Therefore, they can be used and disposed of after a single use. The only problem is that polymer papers cannot be used as recycled materials.
How PE-Coated Papers Differ from Other Coated and Uncoated Papers
Ready to Get Custom Packaging for Your Business?
start with a low minimum order quantity
As discussed earlier, PE-coated papers are types of papers coated with a layer or layers of polyethylene. The layer provides several benefits, including water resistance, moisture resistance, and protection from grease and oils.
There are several differences this type of paper has with other types of coated and uncoated papers. Below are some of these differences.
1. Water and Moisture Resistance
One of the most significant benefits of PE-coated papers is their barrier properties: water and moisture resistance. This makes it ideal for use in products requiring zero or minimal exposure to liquids or humidity, such as food packaging, beverage cups, and medical packaging.
Uncoated and some types of coated papers are not water-resistant and are easily damaged or lose structural integrity when exposed to moisture.
2. Grease and Oil Resistance
Another benefit of polymer-coated papers is their resistance to grease and oils, making them suitable for use in fast food packaging, where food grease can weaken or break the packaging. Notably, many uncoated papers and other types of coated papers lack grease and oil resistance, staining, and soiling when exposed to these substances.
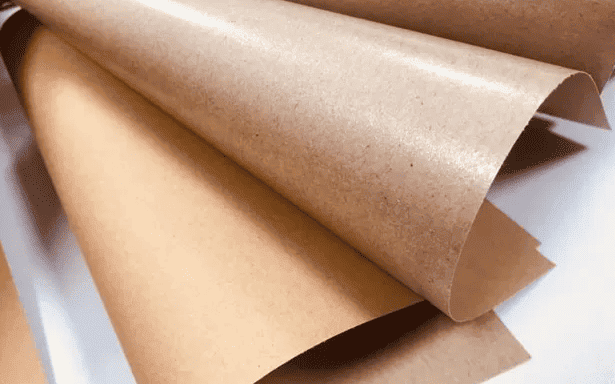
3. Structural Integrity
PE-coated papers have excellent structural integrity with strong barrier properties. This makes them suitable for use in products that require strong and durable materials. It includes items such as paper bags, envelopes, and shipping boxes. Uncoated paper is generally not strong and may tear easily.
4. Printing Capabilities
This type of coated paper is also suitable for printing. Customizing is easy, especially when printing logos, branding items, or other designs. However, it is crucial to note that the coating can make it difficult for some printing methods.
One must choose the most appropriate printing method to guarantee the best outcomes after printing. Uncoated papers and some types of coated papers are generally easier to print on but may not offer the same level of water, moisture, and grease resistance on the final product.
How to Control and Test the Quality?
Due to the varied uses of polymer-coated papers, it is crucial to have quality control measures to ensure that they do not endanger the well-being of consumers. Some of the core issues of concern include quality control, testing, and regulations.
1. Quality Control Measures
- Raw Material Inspection: The first step in producing high-quality PE-coated papers is to inspect the raw materials, including the paper, polyethylene, and other additives used in the production process. Quality control checks the materials for defects, such as tears, wrinkles, or contaminants, and materials with discrepancies are rejected promptly.
- Process Control: During manufacturing, quality control personnel monitor the production equipment to ensure it functions correctly and produces consistent results. They perform regular tests on the finished product to ensure that it meets the desired specifications.
- Finished Product Inspection: After production, the PE-coated papers undergo inspection to ensure that they meet the desired standard. The inspection includes checks for thickness, weight, water resistance, and other core traits.
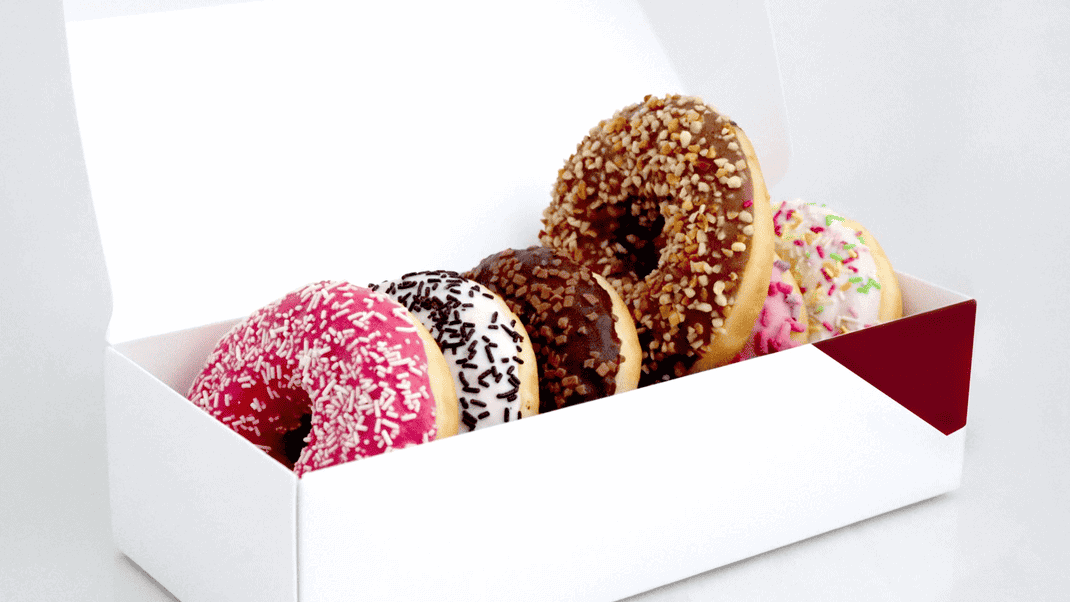
2. Testing Methods
- Water Resistance Test: To test the water resistance of the paper, a sample is submerged in water for a specific period. After the test, the paper is checked for signs of damage or deterioration.
- Grease Resistance Test: A grease resistance test involves exposing the paper to a specific grease or oil type and checking for any signs of staining or damage.
- Tensile Strength Test: This test measures the strength of the paper by applying a controlled amount of force and measuring the amount of deformation or breakage.
3. Industry Standards and Regulations
- FDA Regulations: The Food and Drug Administration (FDA) regulates the use of this paper in food packaging and requires that it meet certain safety standards.
- ASTM Standards: The American Society for Testing and Materials (ASTM) has developed several standards for testing the performance and quality of papers, including water and grease resistance tests.
- European Regulations: The European Union has established regulations for the use of PE-coated paper in food packaging, including restrictions on the use of certain additives and chemicals. These regulations are enforced by the European Food Safety Authority (EFSA).
Quality control measures, testing methods, and industry standards and regulations are essential in ensuring that the paper meets the required barrier properties for optimal performance and safety.
By implementing the measures, manufacturers produce high-quality polymer-based papers that are suitable for use in different applications, including food packaging, medical packaging, and shipping materials.
Conclusion
PE-coated papers are a specialized coated paper type that provides several benefits over other paper types. They are water and moisture-resistant, grease and oil-resistant, and have excellent structural integrity, making them ideal for use in a wide range of applications, such as food packaging, medical packaging, and designing shipping materials.
To guarantee the quality and safety of PE-coated papers, manufacturers implement quality control measures and testing methods and comply with industry standards and regulations. Through this approach, they ensure that they produce reliable and high-quality polymer-coated papers that meet the needs and expectations of customers.
Take Your Business to the Next Level with Packoi
At Packoi, we are committed to offering customers outstanding services, especially packaging designs, printing solutions, and branding. We always seek new technologies and solutions that will make your business sustainable and eco-friendly. If you consider using PE-coated paper in your projects, contact us today for further details and guidance.