Last Updated on April 29, 2025 by Packoi Team
Die-cutting has become a key technique in packaging and printing, offering endless possibilities for creating custom shapes, designs, and functional features.
In this article, we’ll dive into what die-cut holes are, how they are made, their diverse applications, and the various techniques used in die-cutting. You’ll also learn the many benefits of incorporating die-cut holes into packaging and printed materials to enhance both appearance and usability.
What is a Die-Cut Hole?
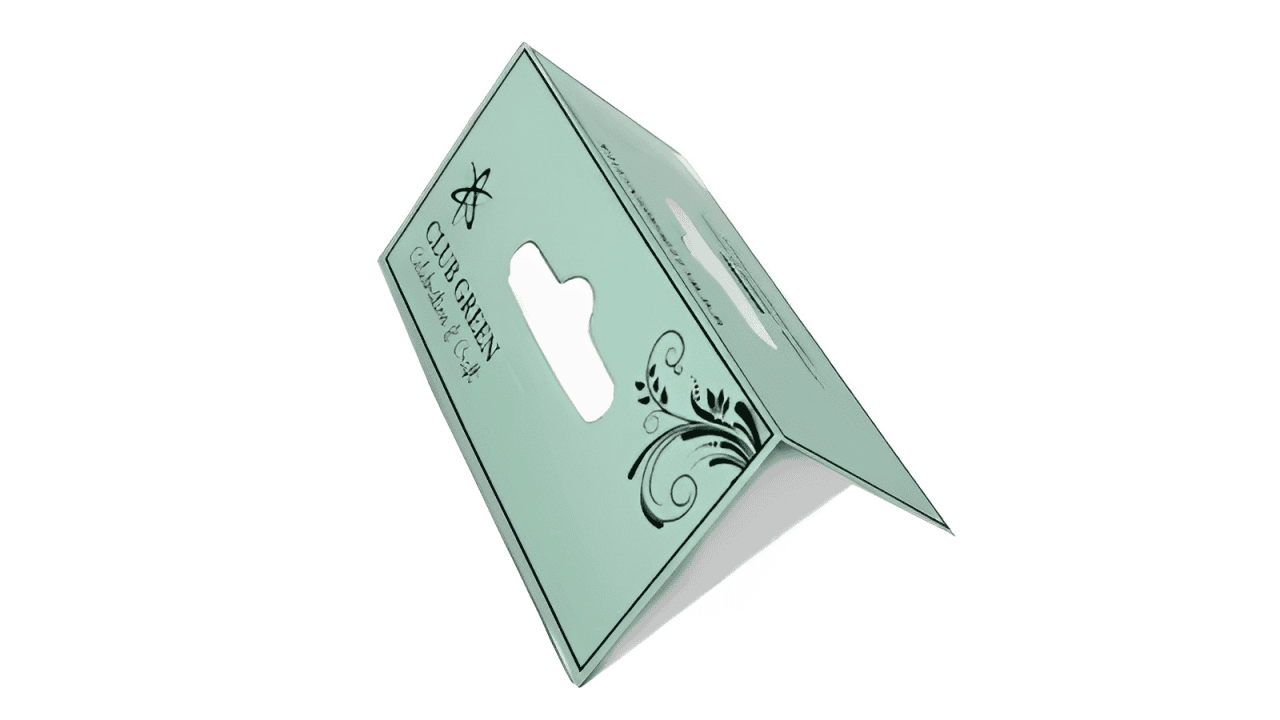
Die-cut holes are shapes or patterns that are cut out of the packaging material to create a unique design. These holes are created using a cutting die, which can be a metal or plastic tool. Die-cut holes come in different shapes, sizes, and designs depending on the requirements of the product.
Applications of Die-Cut Holes
Die-cut holes can be used in a variety of packaging applications such as boxes, bags, labels, and more. In food packaging, die-cut holes are often used for ventilation so the product remains fresh and doesn’t spoil quickly.
In retail packaging, die-cut holes are used for the display of the product. It is often seen in boxes where a part of the product is exposed to showcase the product’s features.
Versatility in Different Packaging Materials
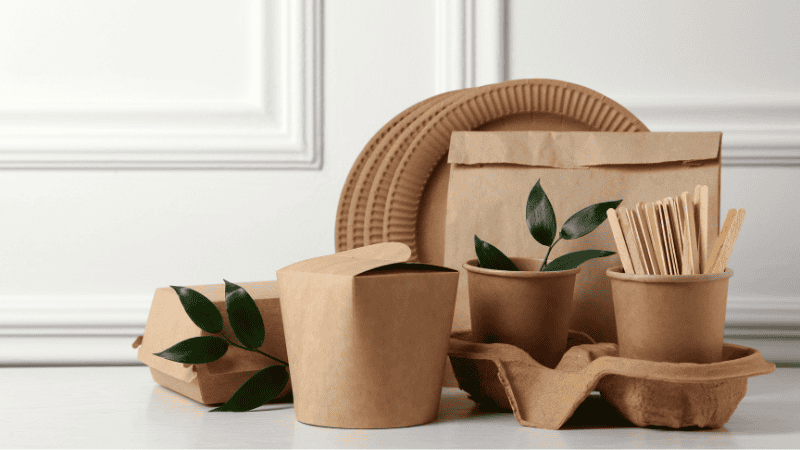
Die-cut holes can be created in a range of materials such as paper, cardboard, plastic, and even metal. The versatility of this technique allows for the creation of unique designs and shapes in a wide range of packaging materials.
The ability to die-cut boxes through various materials opens up new possibilities for creating unique designs that cater to the needs of a wide range of industries.
Die cutting is a process that involves using a die or cutting tool to cut out shapes, designs, or patterns in a material. This process is used in various industries, including printing and packaging, to create custom shapes, sizes, and designs.
Die-cutting plays a vital role in packaging as it allows for the creation of intricate designs, which helps to differentiate products from the competition. Additionally, it provides flexibility in creating custom packaging designs while being a cost-effective solution.
Ready to Get Custom Packaging for Your Business?
start with a low minimum order quantity
4 Types of Die-Cutting Techniques for Printing
There are different types of die-cutting technology and manufacturing techniques now available for printing, each with its own unique benefits. Some of the popular techniques include:
1. Flatbed Die Cutting
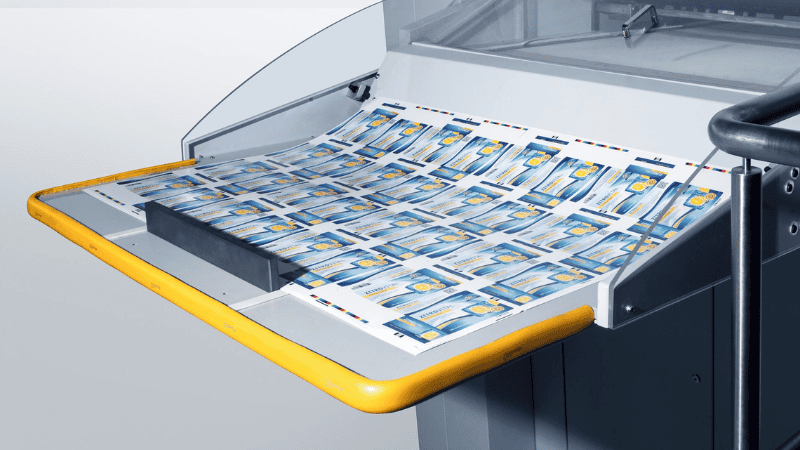
Flatbed die cutting involves using a flatbed die cutter that presses down on the material to create the required shape.
2. Rotary Die Cutting
Rotary die cutting involves using a rotating cylinder with a cutting die attached to it. The material passes through the cylinder, and the die cuts the required shape.
3. Steel Rule Die Cutting
Steel rule die cutting involves using metal, die-cut packaging that has a sharp edge. The die is pressed into the material to create the required shape.
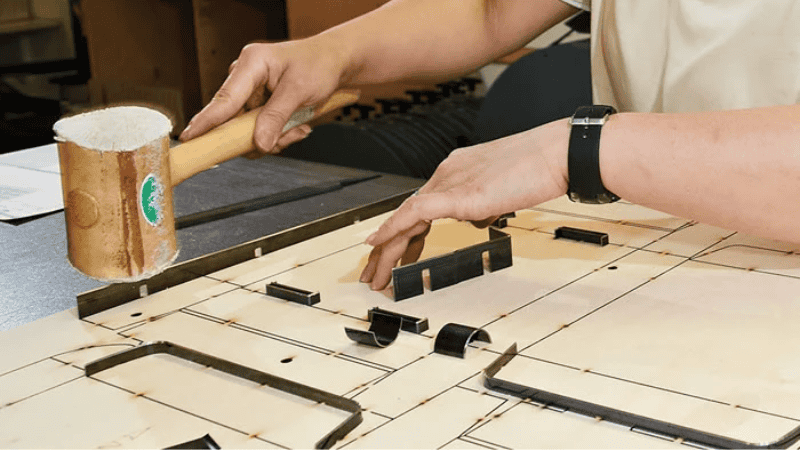
4. Laser Die Cutting
Laser die cutting involves cutting the material into the required shape using a laser. It is a relatively new technique that provides a high level of precision and accuracy.
The Benefits of Using Die-Cut Holes in Printing and Packaging
Die-cut holes have a range of benefits when it comes to printing and packaging. Some of the key benefits include:
In Printing
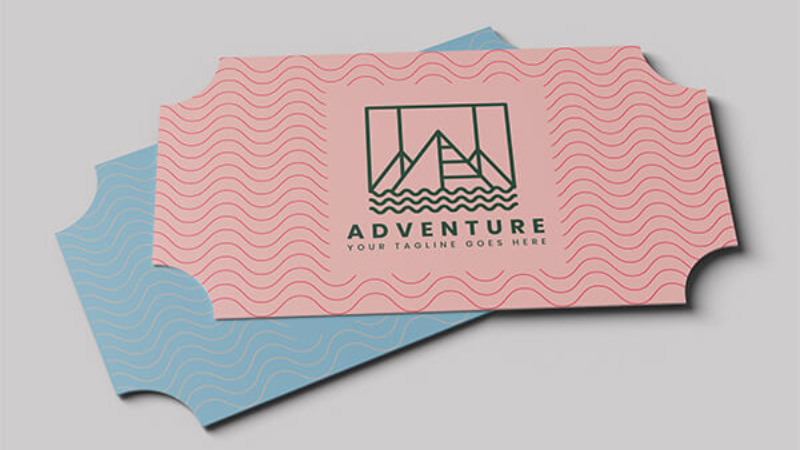
Die-cut holes can be used to create unique shapes and designs in printed materials such as business cards, flyers, and brochures. The ability to create custom shapes and designs adds an extra level of visual appeal to the printed material, which helps to differentiate it from the competition.
In Packaging
Die-cut holes can create unique shapes and designs in packaging materials such as boxes, bags, and labels. The use of die-cut printing and holes allows for the creation of intricate designs, which helps to differentiate products from the competition.
Additionally, die-cut labels and cut holes can also be used to create functional designs that help to improve the usability of the packaging.
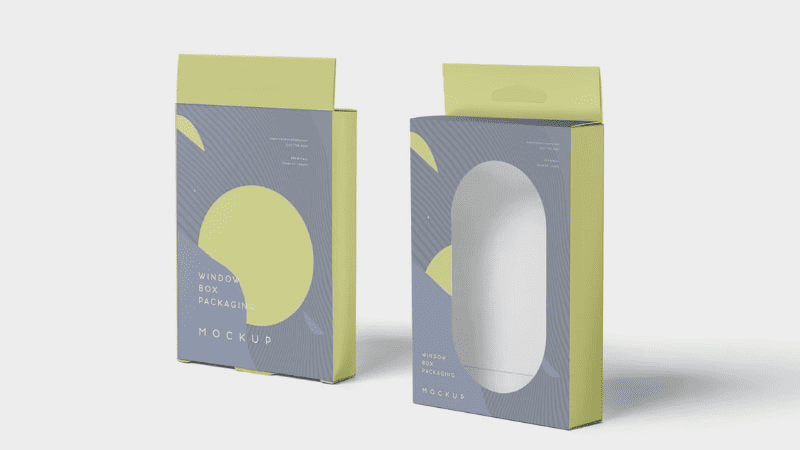
Die-Cut Holes Can Raise the Functionality and Aesthetics of the Packaging
Die-cut holes can be used to create unique designs that cater to the needs of the product.
For example, a die-cut hole in a food package can be used to create a handle for easy carrying or to provide ventilation to keep the food fresh. In this case, the die-cut hole serves a functional purpose, making the package more user-friendly and convenient.
On the other hand, die-cut holes can also be used to enhance the aesthetics of the packaging. For instance, a die-cut hole can be used to create a unique shape or design in a product label, catching the attention of consumers and making the product stand out on the shelves.
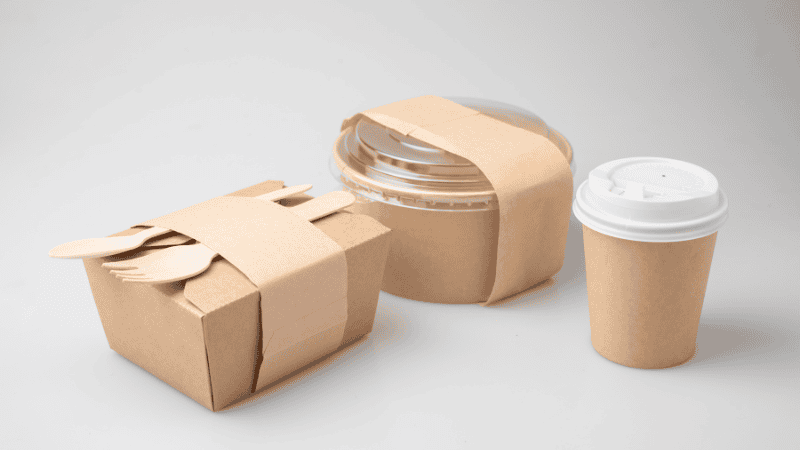
In addition, die-cut holes can be used to create patterns and textures in the packaging, adding a tactile element to the design and making it more visually appealing.
Furthermore, die-cut holes can be combined with other printing and packaging techniques, such as embossing, foiling, and spot UV, to create even more complex and striking designs.
For example, a die-cut hole in a metallic foil package can create a peek-a-boo effect, allowing consumers to see a glimpse of the product inside while also showcasing the shiny and luxurious finish of the packaging.
How is a Die-Cut Hole Created?
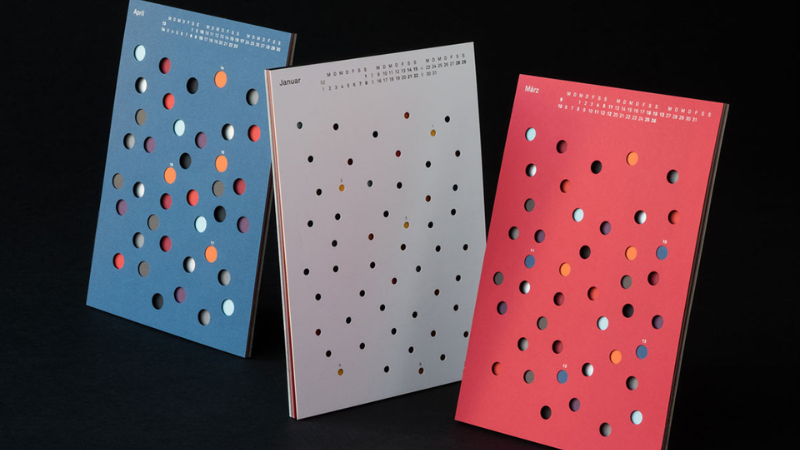
Die-cutting is a process of cutting material into a specific shape using a die. A die is a sharp metal blade that is designed to cut a specific shape or pattern.
Die-cutting is a popular technique in the printing and packaging industry, where it is used to create precise and intricate designs in materials such as paper, cardboard, and plastic.
One of the most common uses of die-cutting is to create die-cut holes, which are holes of a specific shape cut out of a flat material part. In this section, we will explore how die-cut holes are created and the tools and machinery used in the process.
Tools and Machinery Used to Create Die-Cut Holes
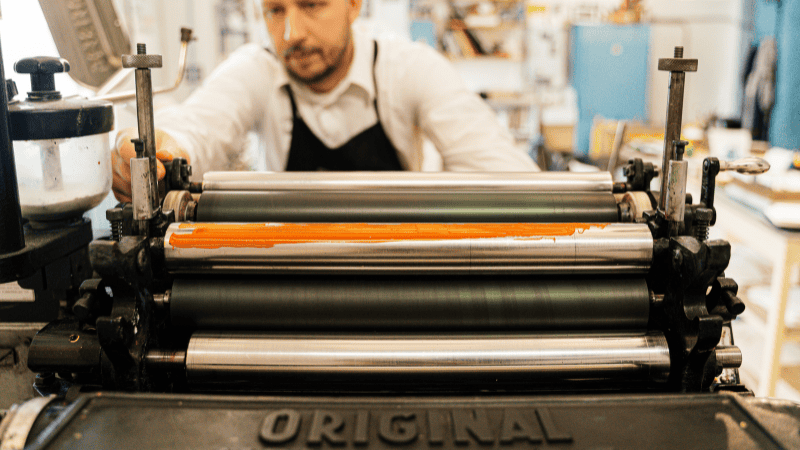
The tools and machinery used to create die-cut holes vary depending on the type and size of the project. Here are some of the most common tools and machinery used in the process:
1. Die-Cutting Machine
A die-cutting machine is a device that is used to cut out shapes from various materials, including paper, cardboard, and plastic. The machine consists of a platform, a cutting board, and a roller system that passes the material through the cutting blade.
2. Die
A die is a metal blade that is designed to cut a specific shape or pattern. The die can be customized to create custom die cutters and in-cut holes of various shapes and sizes, depending on the project’s requirements.
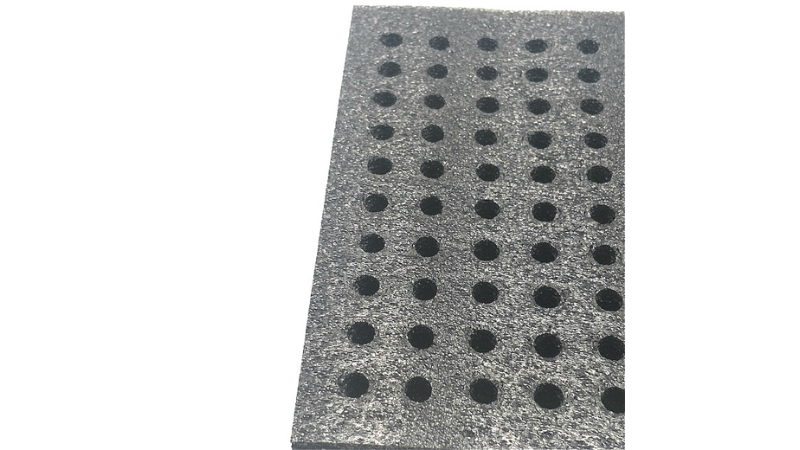
3. Cutting Plate
A cutting plate is a hard, flat, or curved surface that is placed beneath the steel dies of the material to be cut. The cutting plate protects the die and the machine from damage and helps to ensure a clean and precise cut.
4. Adhesive Tape
Adhesive tape is used to hold the material in place during the cutting process. The tape should be strong enough to keep the material from shifting during cutting, but not so strong that it damages the material when removed.
The Process of Die Cutting
The process of digital die-cutting machines begins with the design of the die. The die is created by a skilled designer who uses computer software to create a precise and accurate design. The design is then sent to a die-cutting machine, where the die is loaded onto the machine’s platform.
Once the die is loaded onto the platform, the material to be cut is placed on the cutting plate, and adhesive tape is used to hold it in place.
The cutting plate, die board, and material to be partially cut are then passed through the machine’s roller system, which pushes the material through the cutting blade. The blade cuts through the material, creating a die-cut hole of the desired shape and size.
After the cutting process is complete, the raw material used is removed from the metal dies in the machine and inspected for accuracy and quality. If the die-cut holes are not clean and precise, adjustments may be made to the die or the cutting process to improve the results.
In some cases, additional steps may be required to finish the die-cut holes. For example, the die line or hole edges may need to be smoothed or polished to remove any rough edges. The material may also need to be folded or creased to create a specific shape or structure.
Ready to Get Custom Packaging for Your Business?
start with a low minimum order quantity
Factors that Affect the Quality of Die-Cut Holes
Various factors determine the quality of a die-cut hole. These factors can either enhance or hinder the overall quality of the die-cut process. Some of the main factors affecting a die-cut hole’s quality include pressure, material thickness, and blade sharpness.
Pressure
The amount of pressure applied during the die-cutting process is critical in determining the quality of the die-cut hole. Insufficient pressure may lead to poorly defined cuts or even incomplete cuts, which can lead to improper package functionality.
On the other hand, too much pressure can damage the cutting die and cause irregular cuts. To ensure that the correct amount of pressure is applied, experienced operators typically set and adjust the die-cutting machine’s pressure depending on the material and design requirements.
Material Thickness
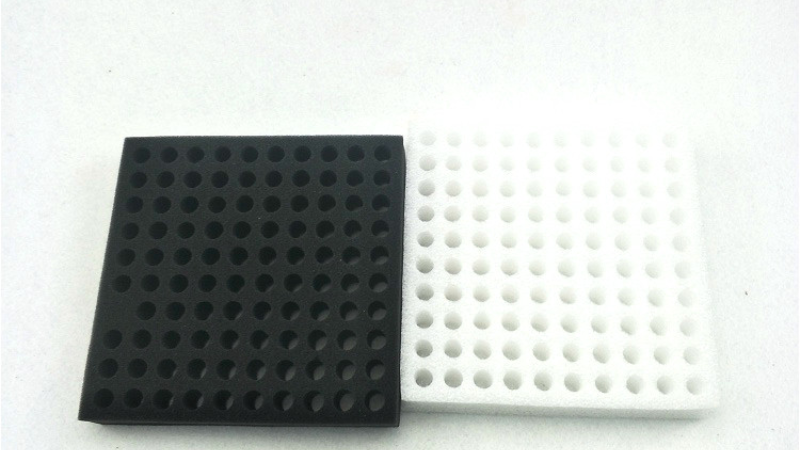
The thickness of the material being cut is another important factor in the quality of die-cut holes. Some materials may require more pressure than others to achieve a clean and precise cut.
When cutting thick materials, the operator may need to adjust the cutting die and the cutting machine to provide enough pressure to cut through the entire material thickness. This ensures that the die-cut hole is clean and properly defined.
Blade Sharpness
The sharpness of the cutting die is another crucial factor in die-cutting quality. A dull cutting die can result in poor-quality cuts and increase the risk of damage to the material being cut.
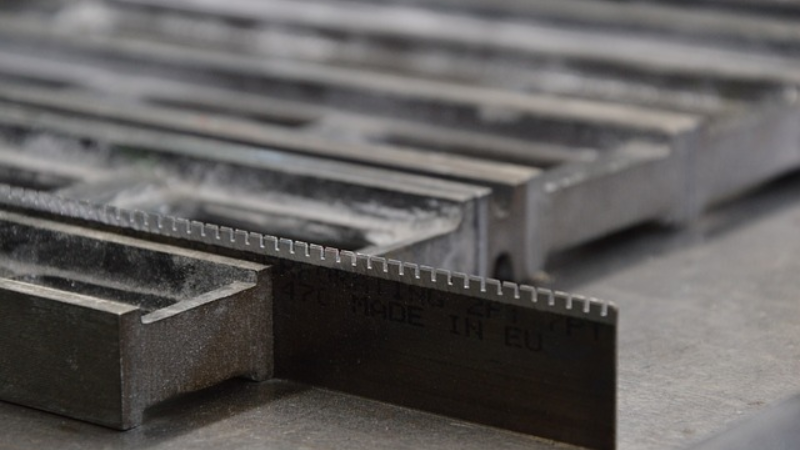
A dull blade may cause the material to tear or rip, resulting in a poor-quality die-cut hole. Experienced operators often check and replace blades regularly to ensure that they are sharp and provide clean cuts.
Other factors that may affect the quality of a die-cut hole include:
- The type of material being used
- The custom die-cut process
- The type of die-cutting machine being used
- The design of the cutting die itself.
Using the correct machine for the material and job at hand is also critical. For example, a rotary die-cutting machine is best suited for high-volume jobs, while a flatbed die-cutting machine is ideal for small-scale jobs or custom projects that require more intricate designs.
Why Should You Care About Precision and Accuracy in Die Cutting?
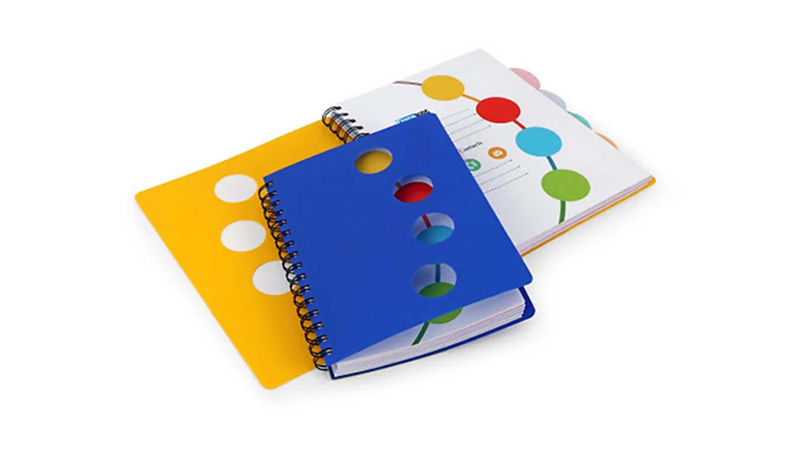
Precision and accuracy are crucial in the creation of die-cut holes. When a die-cut hole is not cut correctly, it can lead to a host of problems, such as damage to the product or ineffective packaging. The use of die-cut holes is not just for aesthetic appeal but also for functionality.
An incorrectly cut die-cut hole can lead to an inability to stack or store products properly, leading to possible damage or inefficiencies. Additionally, if a die-cut hole is not cut correctly, it may not align with the product inside, leading to poor presentation and an overall negative brand image.
Die vs Digital Cutting Methods
Die-cut holes can be used in almost any type of packaging, including cardboard boxes, plastic bags, and labels. For example, in food packaging, the use of a die-cut hole in plastic film packaging can aid in steam release during microwave cooking.
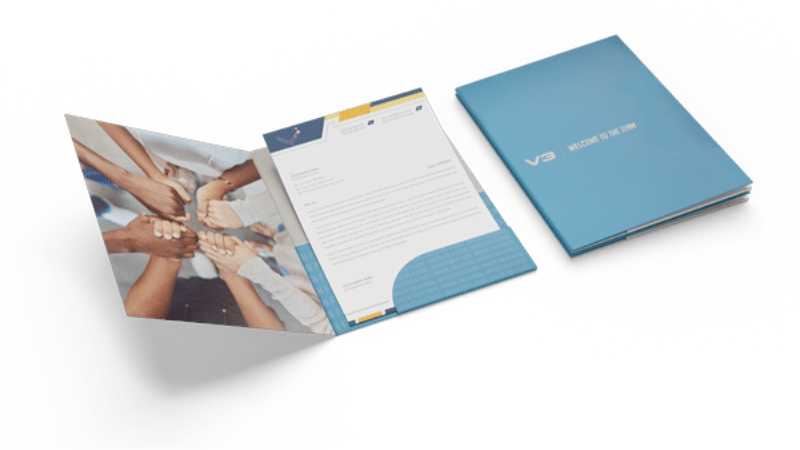
In the cosmetic industry, die-cut holes are used in display boxes to showcase the product, often allowing consumers to touch and feel the product.
Die-cutting has been a popular method of cutting die-cut holes for years, but digital cutting has recently become more prevalent. The choice between digital die-cutting and digital cutting methods depends on the job’s nature and requirements.
What is Digital Cutting?
Digital cutting is the use of computer-controlled machines to cut designs into a range of materials such as paper, vinyl, and plastics. These specialized machines work based on pre-programmed instructions, making them ideal for high-quality, intricate designs, and are useful for small runs.
The Difference Between Die and Digital Cutting
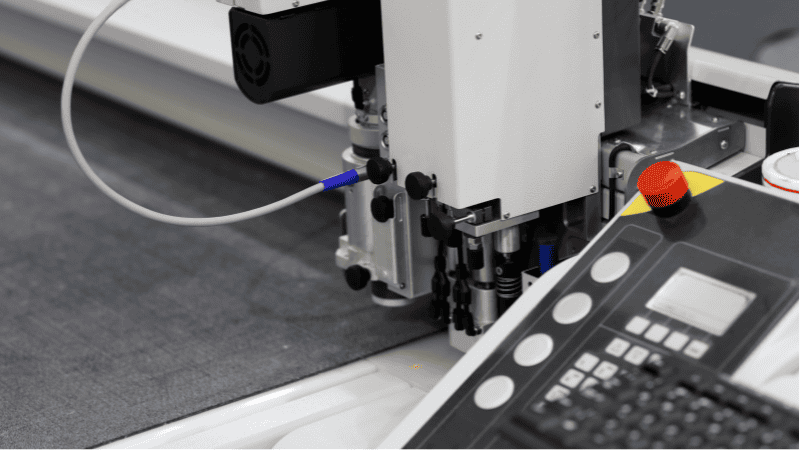
While both methods produce quality cuts, there are differences between the two methods.
Die cutting requires upfront costs to make a die, a physical template guiding the cutting process. On the other hand, digital cutting requires no upfront costs but requires computer-aided design (CAD) software and a digital cutter.
Which is the Better Option?
The choice between manual and digital die-cutting machines depends on the job’s nature and requirements. For short runs or intricate designs, digital cutting is more suitable, whereas for longer runs or standard designs, die cutting is often more cost-effective.
Ready to Get Custom Packaging for Your Business?
start with a low minimum order quantity
Examples that Utilize Die-Cut Holes for Functional or Aesthetic Purposes
Die-cut holes are a popular design element in printing and packaging. They can be used for both functional and aesthetic purposes. Here are some examples of how die-cut holes are used in packaging design and printing:
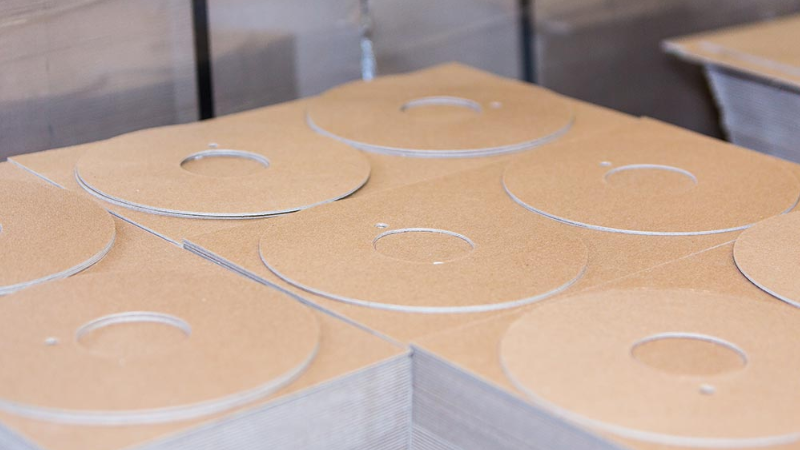
In Packaging
Window packaging – A die-cut hole can be used to create a window in a package, allowing consumers to see the product inside.
Display packaging – A die-cut hole can be used to hang a package on a display hook or to showcase the product in a unique way.
Gift packaging – A die-cut hole can be used to create a unique shape or design in a gift box or bag.
Ready to Get Custom Packaging for Your Business?
start with a low minimum order quantity
In Printing
Business cards – A die-cut hole can create a unique shape or design in a business card.
Invitations – A die-cut hole can create a unique shape or design in an invitation.
Brochures – A die-cut hole can be used to create a unique shape or design in a brochure.
The possibilities are endless for using die-cut holes in printing and packaging. They add an extra level of creativity and customization to your designs.
Conclusion
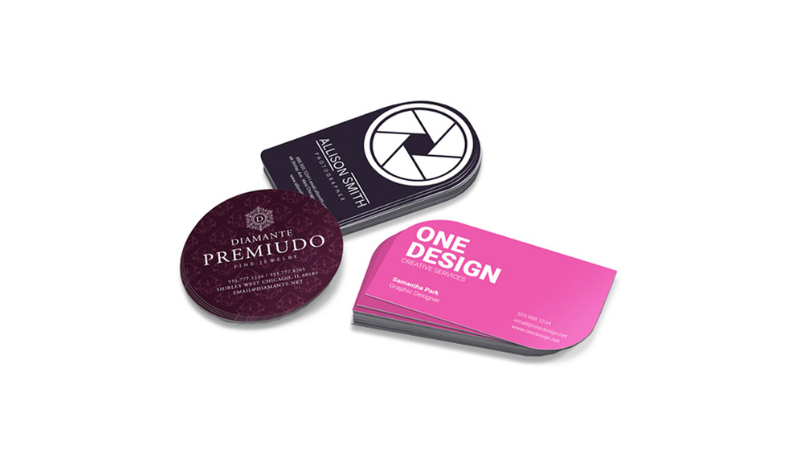
In conclusion, die-cut holes are an important design element in printing and packaging. They allow for unique shapes and designs and can enhance both the functionality and aesthetics of the packaging outline of your product.
Here’s a quick recap of the features of die-cut holes:
Uniformity – Die-cut holes are created using a die, which ensures that each hole is the same size and shape.
Repeatability – Because die-cut holes are created using a die, the same design can be repeated over and over again with consistent results.
Consistent results – Die-cut holes provide consistent results every time they are used, ensuring that your packaging and printing look professional and polished.
Get Printing Services from us
At Packoi, we offer a wide range of printing and packaging solutions that utilize die-cut holes. From boxes to labels to business cards, we can help you create the perfect design for your product.
Ready to take your printing, die boards, and packaging designs to the next level? Contact Packoi today to learn more about our custom dies and die-cutting services and how we can help you create the perfect design for your product.