Last Updated on January 13, 2025 by Packoi Team
Have you ever noticed how brands can have high-quality prints on their packaging? The answer lies in Flexo printing. This printing method stands out in high-volume production and handling of different packaging materials. Flexo printing is thriving as sustainable packaging demand increases. This article unpacks how flexography works and why it’s a top choice for packaging solutions.
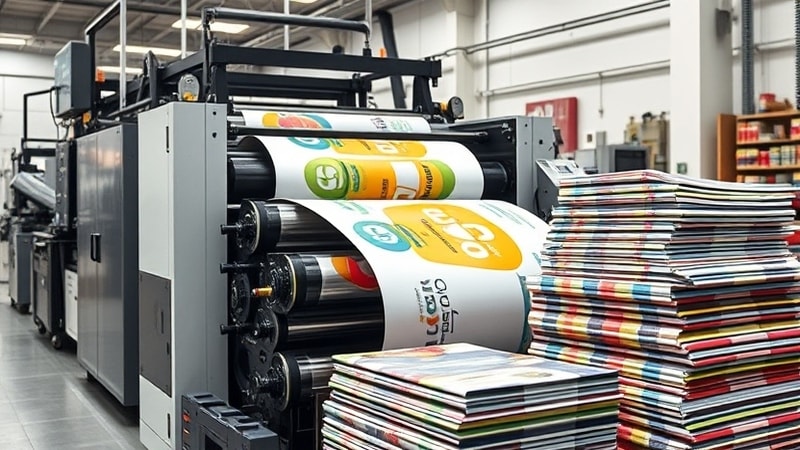
What is Flexographic Printing?
Flexographic printing uses flexible photopolymer plates to achieve high-quality prints and pictures on a variety of surfaces. These rubber plates have raised images that press ink onto the substrates. The flexographic printing plates used are positioned around cylinders on a web press and turn fast in order to deliver accurate prints.
Every color needs its own plate, which contributes to the better quality of the image. Flexo printing allows for a variety of inks to be used in the process, including water and UV inks. It is a desirable and versatile alternative due to its ability to print on a variety of surfaces with a variety of inks.
Flexo printing is compatible with other processes such as laminating, embossing, cold foil stamping, and die cutting. Such combinations enable the formation of new, top-notch custom packaging, which is growing at 5.4% CAGR. This versatility makes flexography the best choice in industries that need customization.
Modern flexography is precise, fast, and can be used for a wide range of applications. Even though today there are many types of prints, flexo printing continues to be the preferred option when it comes to complex designs.
Types of Flexographic Printing Presses
For the types of flexographic printing presses, the main ones are stack press, in-line press and central impression press (C.I. press). Let’s take a closer look.
Stack press
The stack press has a compact design with vertically arranged stations. Most presses have between six and eight decks. The stack press also carries the ability to print on both sides of a flexible plate or substrate in one run.
This press is less precise when used with thin substrate materials though. It is not consistent and, thus, cannot be used for fine prints. But it is compatible with thick substrates.
As a result of its vertical design, the stack press is efficient. The substrates flow rapidly between the stations. Stack press is often used for printing corrugated cardboard and chipboard. The main strength of stack presses lies in their speed and efficiency, especially with thicker substrates.
In-line press
In-line presses are widely used in print houses for commercial packaging. They handle various materials and have six main components. The stations are arranged in a horizontal line instead of vertically. This design ensures a smooth flow of substrates through the press.
In-line presses are great for large print runs. The substrate is pressed between the image carrier and the impression cylinder. Balanced pressure ensures even ink distribution. One major benefit is the variety of colors available. Most setups offer eight colors, but some allow up to 20. This makes it ideal for vibrant and detailed packaging.
Central impression press (C.I. press)
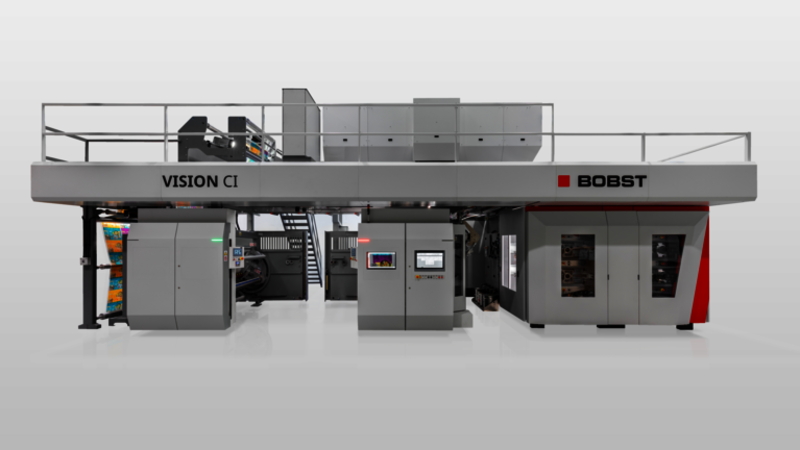
A CI flexo machine is laid down with the stations in a circular pattern with a cylinder in the middle. This arrangement is compared to the planets circling the sun. CI press is suitable for large jobs due to its considerably high capacity.
The most distinctive element of the CI press is the impression cylinder, a single steel drum. During the printing process, it is surrounded by the substrate. This ensures full support while it’s different from other presses where the impression cylinder and the substrate are not supported between units.
CI presses work on large, broad substrates and usually offer six colors. They apply constant pressure and are very low on vibration to ensure quality prints. Some of the benefits include support for multiple materials, high-quality prints, easy-to-make changes, and double-sided printing.
How Does Flexographic Printing Work?
To put flexo printing to work, follow the following steps:
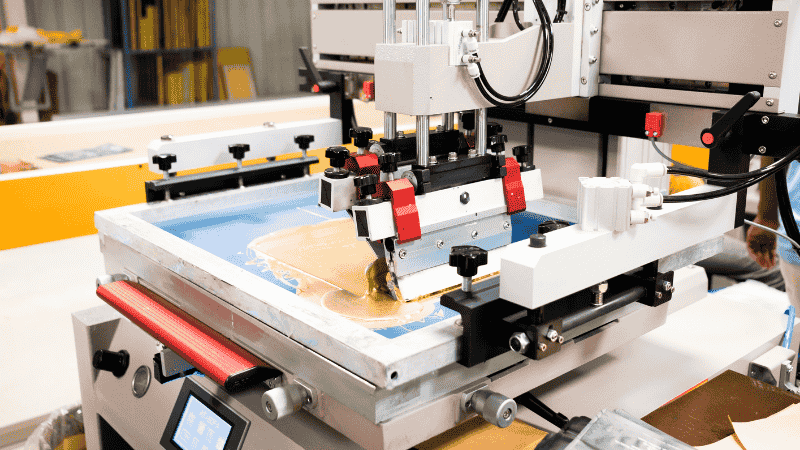
Preparing the printing plates
Flexo printing starts with creating the plates, usually made from rubber or a photopolymer material. These plates carry the design, which is broken into four basic colors: cyan, magenta, yellow, and black. Additional spot colors or varnishes can be used if needed. The plates play a key role in transferring images or text onto the material.
Mounting plates
After preparation, the plates are mounted on the press cylinders. Each color in the design requires its own plate. Precise alignment is required for accurate and vibrant prints. Any misalignment can affect the color matching and final result.
Applicating ink
Ink is delivered to the printing press through ink chambers or ink rollers. Anilox ink rollers control the ink flow, ensuring a precise amount reaches the printing plate. These ink rollers have tiny cells that help transfer ink to the plate evenly. This careful control leads to sharp, consistent prints.
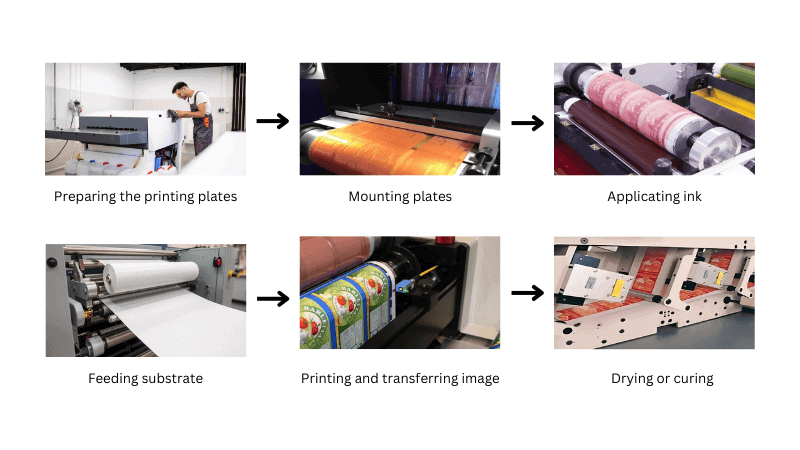
Feeding substrate
The substrate, typically paper, plastic rolls, and solid sheets, is fed into the press. Rollers and tension controls guide the substrate smoothly through the press. This helps avoid misalignment. Proper feeding ensures high-quality prints.
Printing and transferring image
As the substrate moves, the inked flexographic plates transfer the design onto it. Pressure between the flexible printing plate itself and the substrate helps the ink bond effectively. This transfer process is key to producing detailed and vibrant prints. Flexo printing is ideal for fine, high-quality results.
Drying or curing
Once printed, the ink must be dried or cured to set it. Drying can be done with hot air, infrared, UV, or LED UV systems. The method chosen depends on the ink type. This step makes the print permanent.
Tips On The Flexographic Printing Process
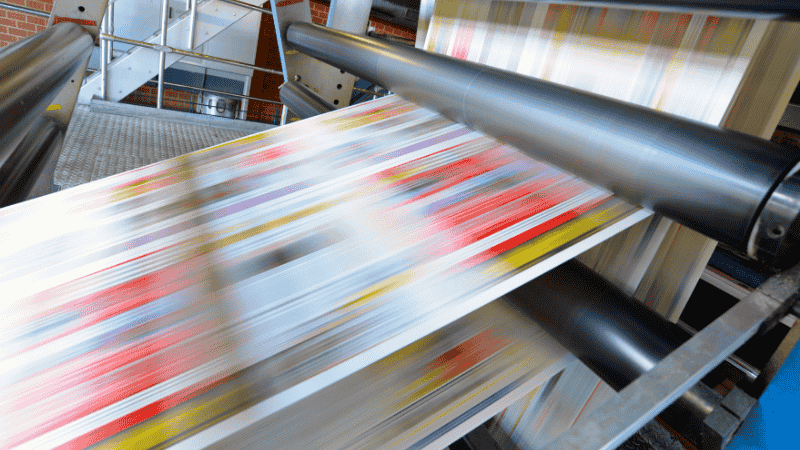
Flexographic printing requires tedious preparation, accurate press setup, and strategic finishing steps to get high-quality output. Each process is crucial to ensure that the end output is accurate, efficient, and visually appealing.
Prepress and Press Set Up
Preparing artwork and images is the first step before flexographic printing starts its operation. The preparation of artwork and images requires attention to detail. The image has to be smaller by a few millimeters than the final size because the elastic plate shrinks when wrapped around the cylinder. This helps to print as intended initially.
The halftone images can be problematic at times as well. The dots may expand during the process of the print and color looks darker or less distinct. To prevent this from happening, the design has to be changed to accommodate the manner in which the dots will change.
In setting up the press, the printing plate is placed on the plate cylinder in which it is used. Then, the setting of inking and pressure are done. This ensures the last print you are going to have is clear and precise, capturing the small details you want to capture.
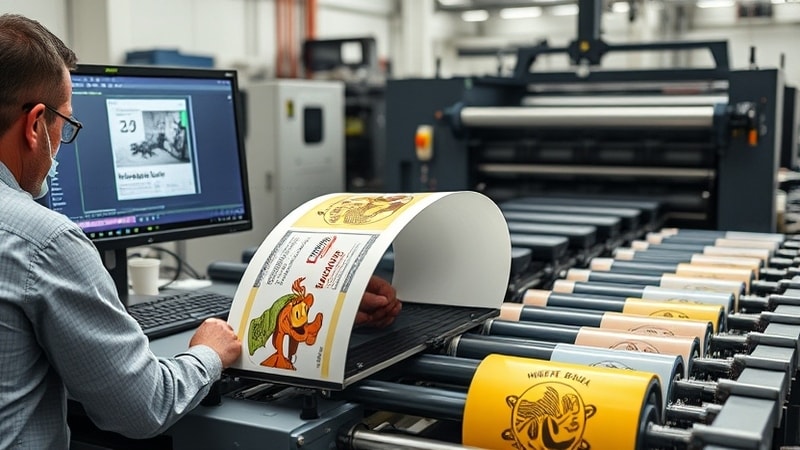
Post-press and Finishing
Additional operations such as die cutting or cold foil stamping and varnish coating can be incorporated directly into in-line presses to increase productivity. All these steps make products neater and presentable without the need to handle them further. Slitting machines are used in the processing of printed materials to cut the full rolls to the right width. This tempers the print quality to exactly fit the required specifications for the subsequent processes.
Secondary processes and the associated equipment, such as folders, gluers, and die-cutters, are put to use to convert printed rolls into packaging products. These are folding cartons, corrugated boxes, and flexible packaging products, among others. It is a very flexible technique and is used for a number of products, including labels, tags, and flexible packaging.
Managing Print Jobs and Workflow
Managing print jobs across various printing methods like flexographic, offset, screen, and even digital printing can be complex. Estimating, scheduling, and shipping a combination of high-volume and short-run jobs require precise planning. Without the right tools, this can quickly become overwhelming.
Ordant’s integrated print-management and web-to-print software simplifies these tasks. It streamlines estimating, scheduling, shipping, and invoicing, helping businesses stay organized. For flexographic printing, in particular, careful planning is crucial for ensuring both efficient production and top-quality results.
Common Applications of Flexographic Printing
1. Packaging
Flexographic printing is commonly used for packaging, including boxes, cartons, and flexible packaging. It allows for fast production and high-quality prints on various materials, making it ideal for packaging needs.
Included among these, flexography is widely used for printing on flexible packaging, such as wrappers, pouches, and plastic films. It is ideal for products requiring flexibility and durability, offering vibrant prints even on challenging materials.
2. Labels
This printing method is perfect for food and beverage labels, stickers, and adhesive labels. It provides sharp, durable prints that maintain color consistency on different types of labels.
This method is also suitable for adhesive labels, enabling precise designs for stickers, barcodes, and tamper-evident seals. The quick-drying nature of flexographic inks allows for efficient production, making it a cost-effective solution for high-volume label printing.
2. Marketing Materials
Flexographic printing is also employed in the creation of marketing materials such as posters, banners, and direct mail inserts. Its ability to handle a variety of substrates and deliver sharp, high-quality prints makes it an excellent choice for producing visually appealing promotional materials at scale.
These materials often benefit from the vibrant color reproduction and durability provided by flexography, ensuring that branding elements remain consistent and impactful.
Advantages and Disadvantages of Flexo Printing
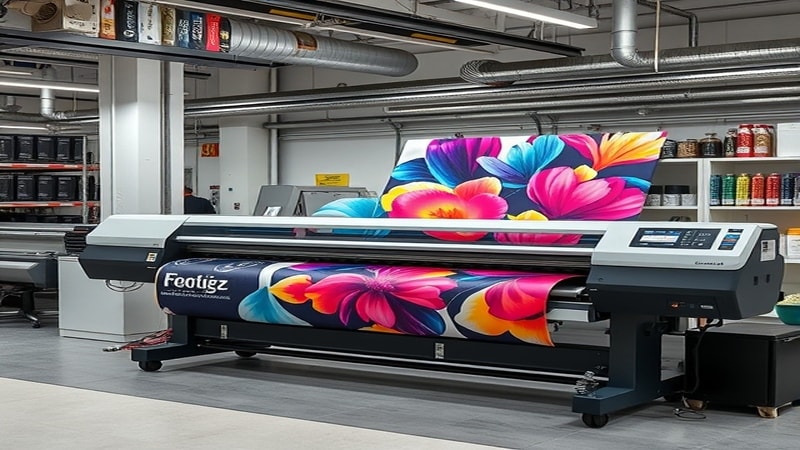
Advantages
- Flexography is characterized by a short production cycle. The setup time is moderate, but the production speed is swift, so it is productive. Servo-based machines provide significant savings in setup time, so short job runs economically.
- Flexo can employ several types of inks including the water-based type up to the UV-curable type, so it is very flexible. It is applicable to paper, board and unsupported film types of substrates.
- The process is fast and highly mechanized, with the least interruption when it comes to the final processes, such as lamination and die cutting.
- Operational costs are low. It is cheap to buy ink and materials, and the per-unit cost is low in the long run.
- Flexo machines are robust, and some of the parts used in them are relatively cheap. They are used to produce good-quality images at a minimal cost per label within one pass.
- Flexo printing is environmentally friendly. Wastewater inks, reusing of inks and energy-efficient drying systems are employed to minimize the environmental effects.
Disadvantages
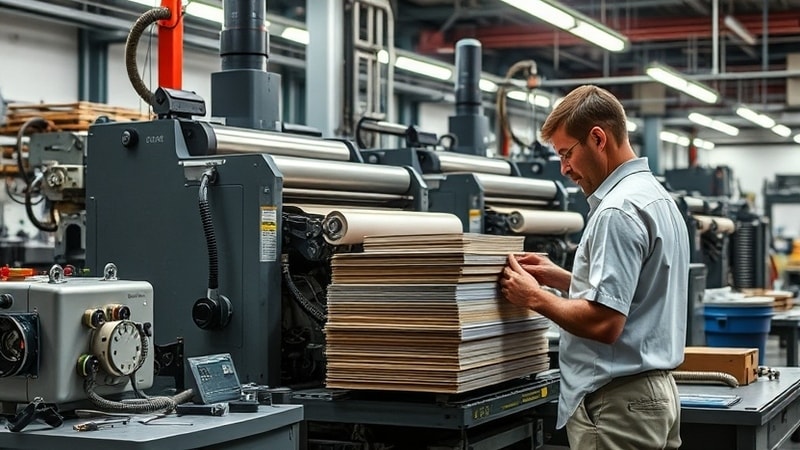
- Flexo printing equipment is sophisticated and always needs to be serviced in order not to call for expensive overhauls.
- The most expensive factors of flexo printing are plates and reprographics. In multi-color production, a plate is required for each color in order to print. As a rule, it is suitable for mid-range to high-volume production because of setup and plate cost.
- The more the number of colors are used, the higher the setup time is. Flexo’s feasibility rests in the ability to meet order volume, setup time, and plate expenses.
Flexographic Printing vs. Other Printing Methods
Flexographic printing technology is suited to high-speed and high-volume print runs. It uses flexible plates to transfer ink on plastic, paper, and aluminum foil, among other materials. This method is widely used for packaging and labeling products. The biggest strength of the flexo technology is its versatility when it comes to substrate compatibility and printing speed.
Flexo printing is more flexible than both offset printing and screen printing and has a faster turnaround time. Offset offset printing is limited to flat surfaces. Screen printing is ideal if you are printing for specific applications like t-shirts, but it’s not efficient for high production. Flexographic printing offers a middle ground, providing a high-speed process, efficiency for diverse applications, and compatibility with a great range of materials.
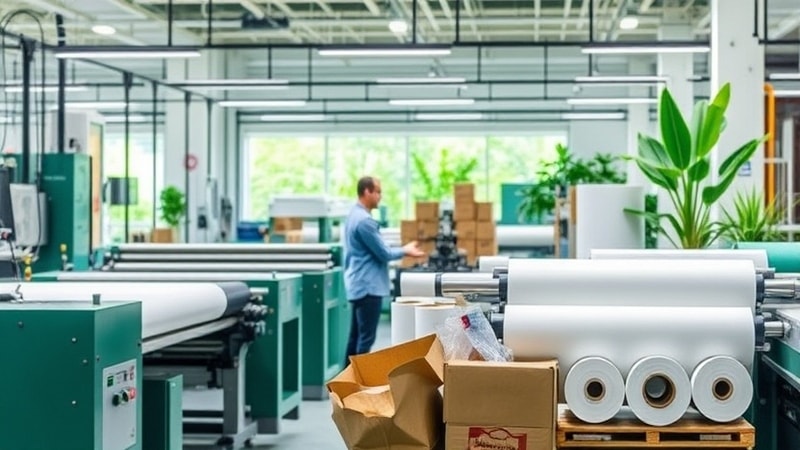
Besides using ecological materials, printers are also trying to contribute to reducing carbon footprint. They are also minimizing wastage and energy consumption right from the production line. One outstanding example is the practice of water-washable flexible packaging plates to address the issue of solvents, which release volatile organic compounds.
Aspect | Flexographic Printing | Offset Printing | Screen Printing |
---|---|---|---|
Applications | Suitable for packaging, labels, and flexible materials such as plastic, paper, and aluminum foil. | Ideal for high-quality printing on flat surfaces such as brochures, booklets, and magazines. | Suitable for printing T-shirts, signage, and custom artwork on uneven surfaces. |
Substrate Compatibility | Highly versatile; works with a wide range of materials, including plastic, foil, and corrugated board. | Limited to flat, stiff media such as paper and cardboard. | Limited versatility, used for textiles, glass, or metal. |
Printing Speed | High-speed and efficient for large volumes. | Slower than flexographic printing, especially for large runs. | Slowest among the three due to the manual setup and ink application process. |
Cost Efficiency | Cost-effective for high-volume print runs but requires initial investment in plates. | More economical for small to medium print runs; setup costs can be high for longer runs. | Ideal for short runs and niche items; less cost-effective for bulk production. |
Turnaround Time | Quick setup and high-speed production ensure fast delivery. | Slower due to extensive prepress setup and plate preparation. | Long setup time and slower print speeds. |
Environmental Impact | Focus on sustainability with water-washable plates and recyclable materials. | Less eco-friendly; traditional inks and processes produce more waste. | Varies often uses solvent-based inks that can have environmental consequences. |
Trends and Innovations in Flexographic Printing
Flexographic printing is an industry, which has started experiencing the changes brought by automation. Currently, most printing presses ranging from narrow web print sector to mid-web, wide-web, inline, and CI presses are all automated. They enhance efficiency, and quality and also reduce costs throughout the whole printing process and production.
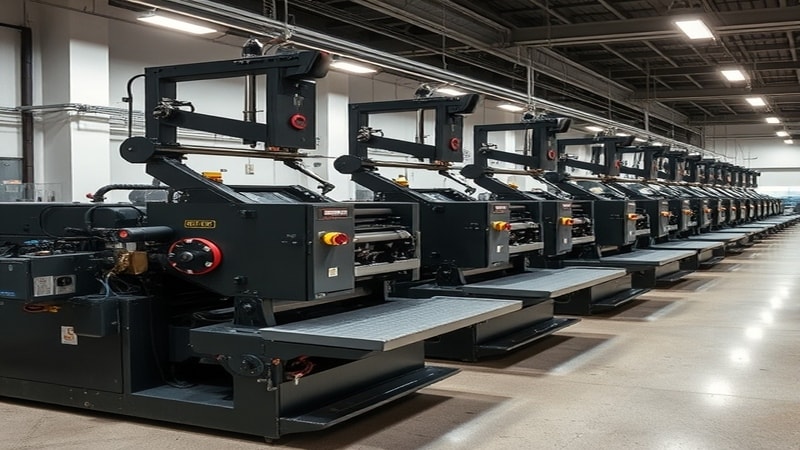
Another of the innovations is digitalization. It enables printers to replace old equipment offered by other manufacturers, thereby making their work more efficient. The flexo plate mounters have gone digital, and many existing flexo machines contain digital interfaces that, in one way or another, diminish the effort of the operator and enhance overall manufacturing quality.
Sustainability is an increasing concern in the flexo printing industry. The industry started using biodegradable products such as water-washable plates to avoid the use of harsh solvents and chemicals.
Conclusion
Flexographic printing is a versatile and cost-effective method, especially for non-porous substrates like food packaging. It offers high production speeds, low waste, and excellent print quality, making it ideal for long-run jobs.
With technological advancements and the use of eco-friendly inks, the flexographic printing process is becoming more popular. It is an excellent choice for both packaging design and label printing, offering businesses a reliable and efficient solution for their printing needs.
Get Expert Advice on Printing Methods with Packoi Printing
Researching printing techniques is crucial for your brand’s packaging. Each option has unique benefits. Let Packoi Printing guide you in choosing the best technique for your needs. Contact us today for expert advice and a fair quote.