Last Updated on April 29, 2025 by Packoi Team
Die cutting is a common term in label printing, especially for custom shapes or intricate logos.
This process uses die-cutting plates or digital machines to shape materials. Modern digital die-cutting relies on a computer-controlled knife guided by a cut file to create precise cuts, whether partial or full, on various materials like labels, gift boxes, or embossing folders.
Unlike traditional dies, digital die-cutting offers more flexibility, lower costs, and faster turnaround. Some machines even include built-in cameras to adjust cuts in real time, ensuring perfect alignment with printed designs.
What Are the Benefits of a Die-Cutting Machine?
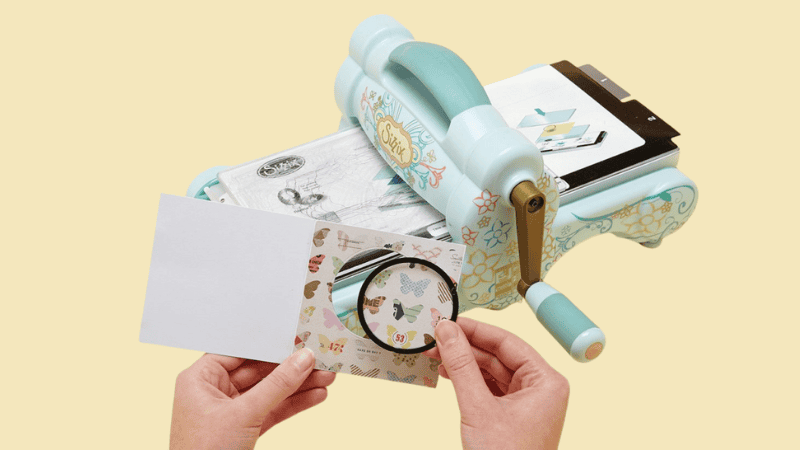
Die-cutting machines, also known as card-making machines, are cutting-edge technologies with sharp edges that cut forms out of cloth, paper, chipboard, and other materials. Most regular die-cut users use personal die-cutting appliances roughly the size of a small microwave oven.
The machines can be stowed in a tiny place and taken out when needed, or they can sit on your crafting table or workspace. These are some benefits:
1. Uniformity
The die cut produces many identical forms based on the die form. Cutting forms around the stock material with more variations than the same pieces.
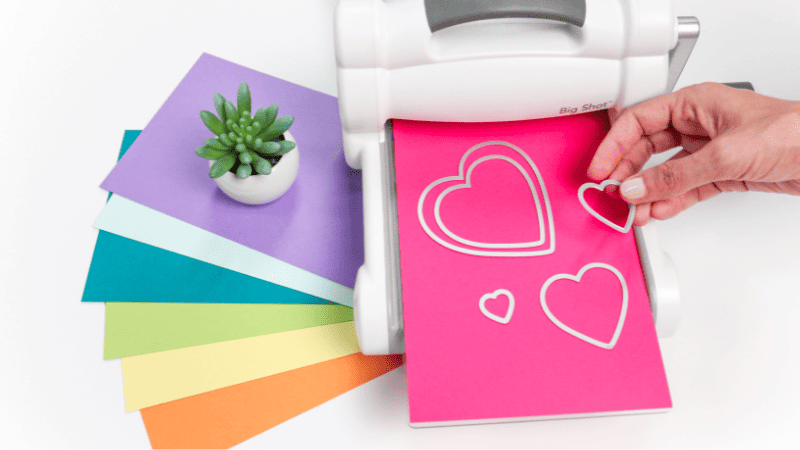
Uniformity is critical for most mass manufacturing applications, including cutting out material box forms, plastics for making electronics and toys, and manufacturing vinyl lettering. In addition, it saves on excess material and an embossing folder.
2. Speed
Because a die-cut machine can construct a shape with a single punch from the cutting plates, it can produce many identical forms quickly, so you can get creative with die-cutting designs on product boxes.
Even a manual die cutter generates shapes significantly quicker than cutting out designs by hand, generating complex shapes that could take a lot of time by hand.
Die-cutting machines can cut loads of identical forms simultaneously, and metal sheets or plastic can be processed through the machine quickly, allowing for speedy output.
3. Low Cost
Other cutting approaches necessitate using many utensils or machines; die cutting is economical because the shapes are created by only a single computer-aided design and machine. Making parts is significantly more efficient with complex die-cutting, reducing labor time.
4. Reduced Waste
Because the dies may be lined up very accurately with the cutting plates, die cutting produces less excess material around the shapes than other procedures. Decreasing waste saves money and is better for the ecosystem.
Ready to Get Custom Packaging for Your Business?
start with a low minimum order quantity
5 Die-Cutting Methods
Various techniques are also used in the die-cutting process. These technologies create a whole new world of structural design possibilities and enable a genuinely personalized packaging experience.
There are several die-cutting processes, such as;
- Blanking: Blanking is the process of slicing a flat piece of material by cutting it from the outer edge. It is a precise degree of flatness.
- Drawing: Drawing involves pulling a substance to a particular length. It is used to create lean and lengthy packaging.
- Forming: The act of molding raw materials onto a curved surface is known as “forming.” It is usually used with a sketch to create rounded, cylindrical objects.
- Coining: Creating circular holes in materials using a hydraulic press to generate careful and elaborate structural design details.
- Broaching: The use of many huge rows of cutting teeth to cut materials that are normally too hard or thick to cut.
The list above shows that the die-cutting procedure can be applied to any packaging material!
What Are Some Common Applications for Die-Cutting in Printing?
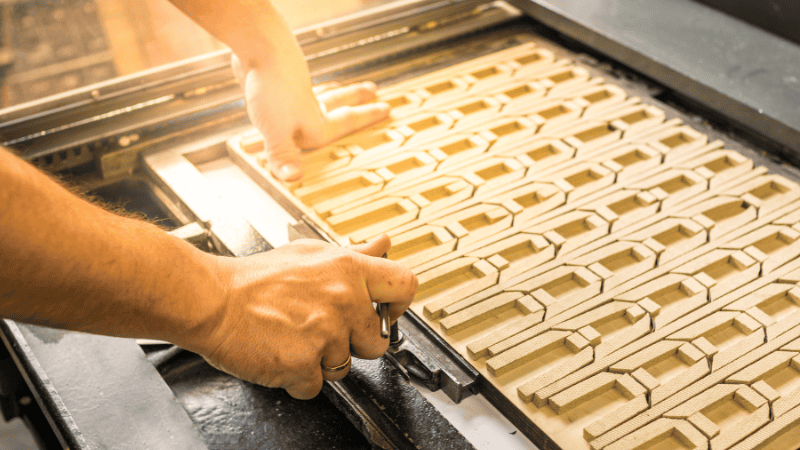
The fundamental objective of a die-cutting device is to create a clean, excellent, and even cut pattern with enough pressure. Manual or automatic cutting machines are available with minimal presses or high-end automatics.
The form of cutter used is determined by the project’s complexity, single or multiple layers, thicker materials, or single stress points, and the substance being used.
Lower die-cutting pressures are more suitable for delicate materials such as paper and cardboard. Cutters can be rotary, as in customary in-line printing beds, or flatbed, as in production runs. Flatbed die-cutting is more economical but slower.
1. Manual Die-Cutting Machines
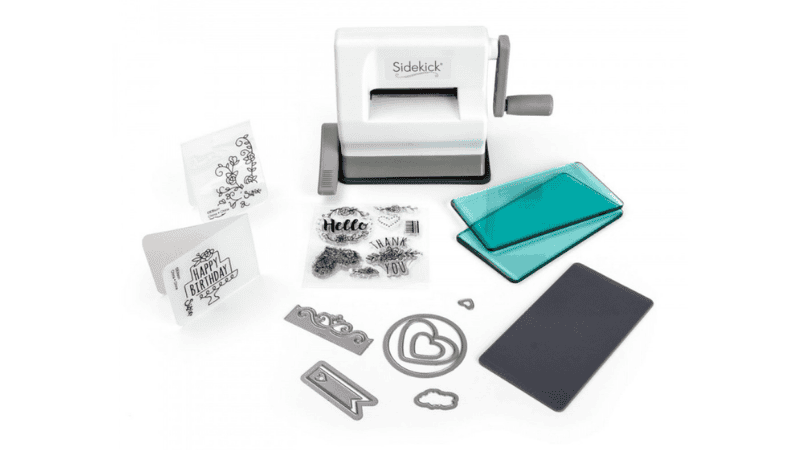
A crank powers the rolling base for manual cutting machines. The crank moves the base to begin die-cutting, and the material is positioned beneath the die-cutting blade as a die-cutting sandwich with the pressure of manual machines.
The material is pressed, chopped, or stamped. Manual cutters are typically used for stamps or labels or for stickers for quilting and scrapbooking. Few machines can create exquisite lace designs as well as little prints. Presses are typically supplied with pre-made metal dies.
2. Automatic Die-Cutting
Automatic cutters are computer-powered designs with sharp blades to cut any stock material with magnetic cylinder steel dies. It is frequently connected and operated similarly to printers or scanners.
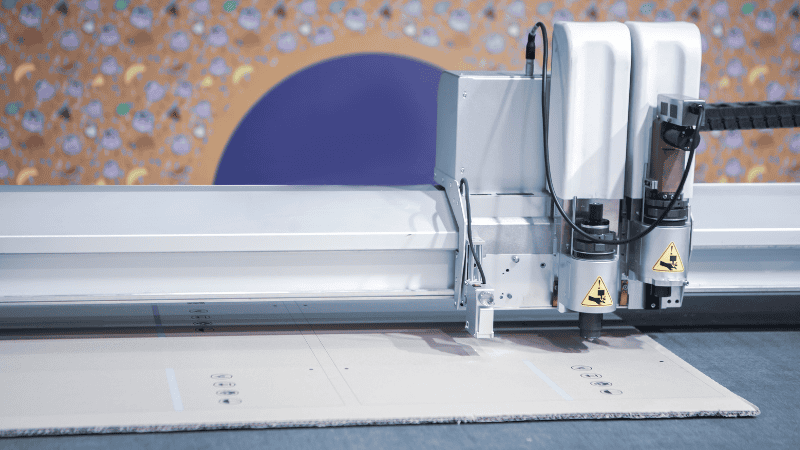
The process includes placing the supplies before the die-cutting sandwich on sticky paper so they do not move throughout the die-cutting procedure.
High-end machines enable computerized saving of pre-loaded images in Vinyl writing/template design, engraving, scrapbook pages, perforating, and embossing a greater range of other materials, including textured and heavier textiles, perfectly normal leather, sheet metal, and other materials.
The Versatility of Die-Cutting
Generally speaking, die cutting, because of its metal shapes and adaptability, is one of the most widely used manufacturing techniques employed in various sectors for a wide range of applications.
There are multiple die-cutting methods, like rotary die cutting, cookie cutters, semi-rotary die cutting, flatbed die cutting, and rotary presses. Here are some examples of how die-cutting may be used to turn everyday materials into valuable things.
- Die-cut shapes for fiberboard materials are utilized in various packaging supplies, such as bookends, envelope mailers, product packaging, and truck and cargo liner components.
- Foam die-cutters can be used to make a variety of automobile parts, including gaskets and car padding.
- Die-cut plastic could make various items, such as hold-downs and stiffeners.
- Die-cut rubber has several automotive purposes with its stock material and is commonly used to make sheet gaskets, pump gaskets, gasoline engine seals, and electric motor gaskets.
- A wide range of fabrics, including felt, polyester, cotton, and carbon fiber, can be processed with die cut and used in car parts like car seat inserts, padding, and door fabric inserts.
Ready to Get Custom Packaging for Your Business?
start with a low minimum order quantity
7 Tips to Choose the Right Die-Cutter for Your Business or Project Needs
Die-cut tools should be chosen with consideration. Before purchasing a die-cutting machine, conduct extensive research to guarantee that the instrument matches your requirements. Before you acquire the instrument, there are a few things you should take into account.
Below are the elements you should consider when choosing the machine:
1. Type of Die-Cutting Machine — Manual or Digital
Looking for tips on buying a die-cutting machine? The first item on the list of critical considerations is the type of equipment. Die-cutting machines are classified into two types: manual and digital.
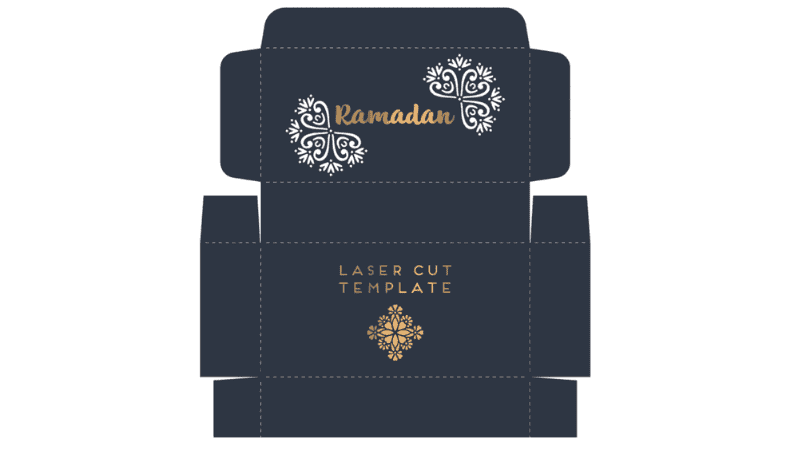
A hand crank with flatbed die cutters or kiss cutting is used in a manual die-cutting machine that uses pressurized force to cut the material through a slot. The material is embossed or sliced in a partial cut. Such tools are highly inexpensive and portable.
2. Manual Die-Cutting Machines
Although manual machines are less expensive as an initial outlay, their long-term operating costs may be higher due to the cost of separate dies.
However, the simplicity of using the many different dies that are readily accessible and that coordinate with their preferred stamps may make stampers who don’t know about die-cutting adore manual die-cutters.
Using plastic embossing folders, this die-cutter can emboss sheets and thin metal, a feature that digital machines lack. Manual cutters can also effortlessly cut various materials using steel rule dies.
3. Digital Die-Cutting Machine
A digital die-cut machine operates similarly to a printer for cutting materials. Cartridges, which link to a computer or plug into the equipment, are used in this type of equipment.
If you wish to develop personalized designs, try to buy die-cutting machines that link to a computer. All digital cutting die machines don’t let you generate bespoke designs; thus, ensure that the machine’s software lets you accomplish the die-cutting process easily.
4. Cost
Regarding die cutters, manual devices can cost as little as $50, while heavy-duty equipment can cost $1,000 or more. When purchasing die-cutting equipment, it is critical to consider your needs.
Businesses and professional artists may consider going for superior equipment. It’s usually preferable to opt for a quality machine that costs somewhat more than settling for a cheaper model, which may be problematic.
Other considerations include the cost of dies, new blades, accessories and equipment, cartridges, and cutting mats that may need to be replaced. Professional software versions or updates may increase the cost of a die-cutting machine.
5. Material and Versatility
Consider the types of materials you would use and the projects you would construct using a die-cut machine. Do you want a rotary die, a semi-rotary die, a flatbed die, or a cylindrical die? Now, consider if you want intricate dies, metal shapes, flexible dies, solid dies, steel rule dies, or something else.
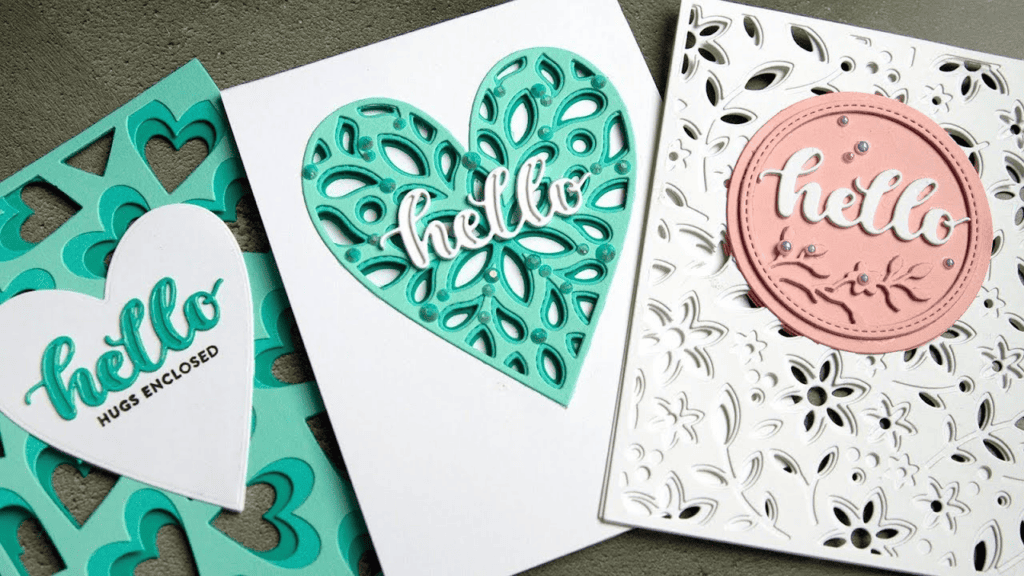
Heavy-duty machines can cut through a more extensive range of materials. Investing in a heavy-duty tool makes no sense if you cut primarily using paper-based materials. The equipment’s adaptability should also be considered. Other than cutting, you may need abilities like embossing and drawing.
6. Ease of Usage
Even if you have high-quality die-cutting equipment, you may find using the machine’s software challenging. You might have a steep learning curve, or there isn’t enough assistance, and ultimately, you die. A good suggestion is to research the software accompanying the computer and see the types of tutorials offered.
Additionally, research the firm from which you intend to purchase the machine and get flexible dies. Several companies have lessons, email, phone support, and forums to help you get a good start at die-cutting.
7. Dimensions and Portability
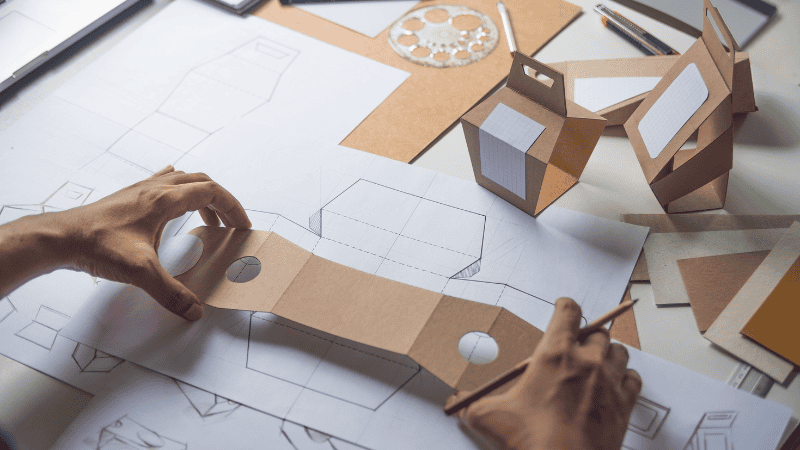
Portability and compactness may also be crucial considerations when checking for die cuts. Is your working area small? Then it is better to begin die-cutting using a service provider.
If you intend to travel with the die-cutting machine, you must also consider its weight. Die-cutting machines can weigh as little as 2 pounds and as much as 40 pounds, with many metal dies.
Ready to Get Custom Packaging for Your Business?
start with a low minimum order quantity
Conclusion
The die-cut process makes custom packaging easier for businesses and manufacturers. While the initial set-up cost can be expensive for some, especially if you need just one rotary die or kiss cutting with steel rule dies,
So why bother buying a die-cutter when many companies provide the die-cutter service? By getting one, you don’t have to face the disadvantage while ensuring the quality of your die-cut shapes in mass production is according to your standard.
Credible companies will also offer various functions and methods to choose from. From basic shapes to intricate shapes in any material you want, from the mechanical press to high-tech magnetic cylinders and more
If you plan on buying your die machine with a specific cutting head and die inside, make sure to utilize your die-cutting machine to its maximum potential by choosing one that matches your production needs. Consider machine size, ease of use, materials you typically employ, and volume and speed needs.
Get Your Perfect Die-Cutting Design With Packoi Today!
If you’re still undecided about getting a die-cutting machine or getting a company to do it for you, Packoi Printing will assist you. We provide a variety of cutting-edge die-cutters and other packaging tools. Just tell our specialists your requirements, and we’ll devise a plan that fulfills your criteria.
Get creative with your stock packaging from Packoi Printing and get the packaging your business needs. Our skilled staff can help you select the most cost-effective way to finish your project, from foil stamping and die cutting to embossing and inventive pocket folders.