Last Updated on January 2, 2024 by Packoi Team
Are you wondering about the difference between heat-set ink and UV-cured ink in the printing industry? Well, I’ll tell you today. These two inks are very popular among printers, and they have different characteristics.
Thermosetting inks rely on chemical reactions and heat drying, while UV-curable inks undergo photochemical reactions when exposed to ultraviolet light. This difference affects ink chemistry and how it behaves on different surfaces, such as paper, ink film, or other materials.
So let’s dive, from water-based inks to solvent-dry ink that is dry to the touch, into everything you need to know about thermosetting inks and UV-curable inks!
What Is Heat-Set Ink?
Heat-set ink, also known as an ink film special drying ink, is a type of ink that is specifically designed to be dried using high temperatures, medium pressure, and forced air circulation.
It is commonly used in water-based and solvent-based inks for commercial printing and packaging applications, along with UV inks and latex inks.
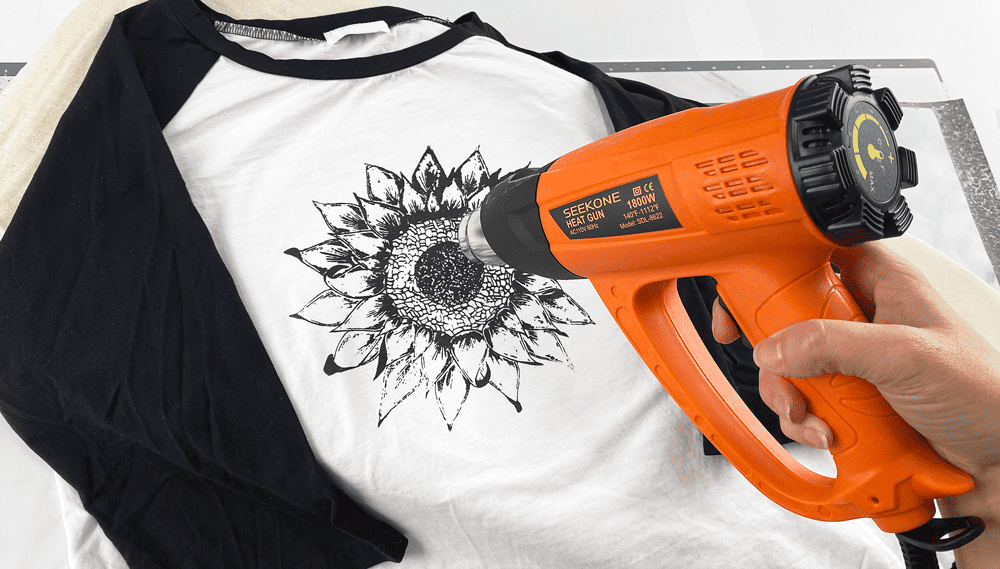
Here are some keys for heat-set inks:
- Characteristics: Heat-set ink dries fast because it has solvents that evaporate when it gets hot. It flows easily through the printing press because it’s not too thick. The ink also has pigments that make the colors bright and the prints look good.
- Drying Process: Heat-set ink is applied to the surface using a printing press. Aqueous coatings and resin help the ink stick to the plate. This makes the print strong and colorful. After printing, the material goes through a hot oven. This is for ink printing, like screen printing and LED printing. The oven has air circulation to dry the ink quickly.
- Applications: Heat-set ink is used in commercial printing for magazines, catalogs, brochures, and newspapers. It can be made better by adding aqueous coatings, which make it stronger and look nicer. These coatings are usually made of resin and can be applied with a press or screen. Heat-set ink is also used in packaging for things like food containers, labels, and flexible packaging. This type of ink is often used with screen-printing ink and solvent ink.
Ready to Get Custom Packaging for Your Business?
start with a low minimum order quantity
Pros and Cons of Heat-Set Ink
Pros
- The quick drying time of screen printing inks allows for faster production speeds on high-volume print runs. This is especially beneficial for ink printing processes that require efficiency and productivity. Additionally, screen printing with silicone can further enhance the performance and quality of the prints.
- The use of heat enables better adhesion to various substrates, ensuring durability in aqueous coatings, printing inks, screen printing ink, and screen printing silicone.
- Heat-set ink, used in screen printing, provides excellent color saturation and sharpness for vibrant prints. This type of ink is commonly used in the printing industry alongside other types of printing inks, such as aqueous coatings and silicone.
Cons
- The need for specialized equipment, such as drying ovens, in the printing industry can increase production costs for printing inks and aqueous coatings.
- Solvent-based heat-set inks may emit volatile organic compounds (VOCs) during the drying process, especially when using aqueous coatings, UV coatings, or screen printing. Additionally, the use of silicone in these inks can also contribute to VOC emissions.
- Certain substrates may not be suitable for heat-setting due to their sensitivity to high temperatures. This can be a concern when using printing inks, especially screen printing ink, as well as aqueous coatings and silicone.
What Is UV-Cured Ink?
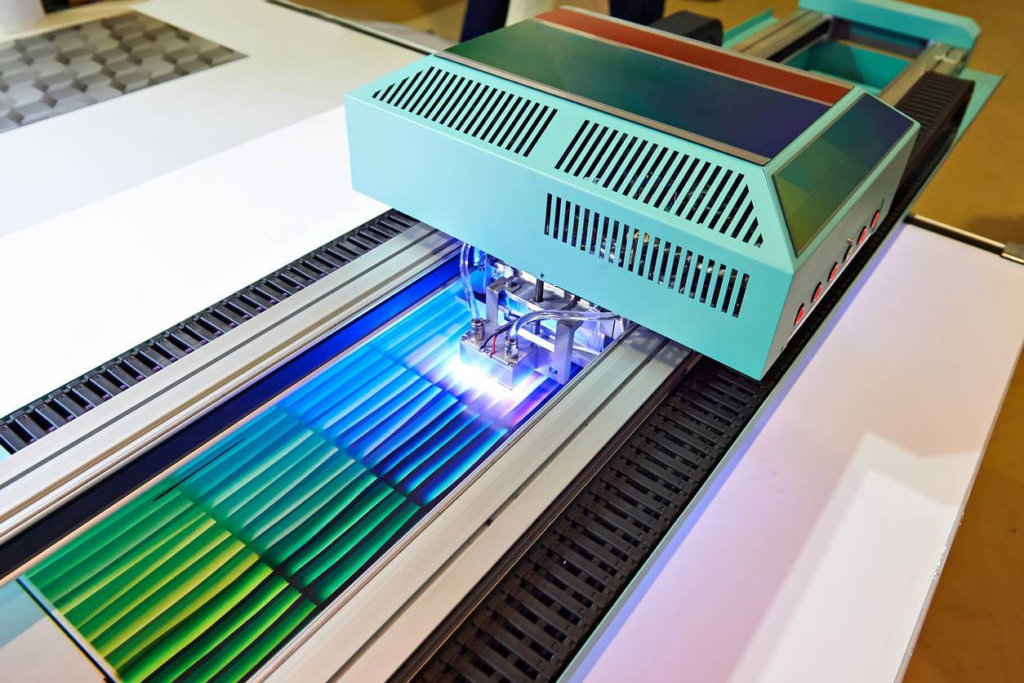
UV-cured ink, also known as UV ink or UV printing ink, is a type of fully cured ink that offers unique properties and benefits compared to traditional heat-set ink. This innovative ink is a fully cured ink made instantly through exposure to ultraviolet (UV) light and is commonly used in various industries. Its defining characteristics include the use of photoinitiators and aqueous coatings, as well as chemical-resistant properties such as the incorporation of silicone for improved performance.
- Definition and Properties: UV-cured ink is formulated with special photoinitiators that react when exposed to UV light, initiating a rapid polymerization process. This process causes the ink to dry and harden almost instantly. As a result, printed materials using UV-cured inks can be handled immediately without smudging or smearing.
- Instantly Cured with Ultraviolet Light: UV-cured inks dry instantly using ultraviolet light instead of waiting for evaporation or absorption. UV lamps during printing cause a chemical reaction that turns the ink from liquid to solid in seconds.
- Application: UV-cured inks are popular in many industries because they can cure quickly and work well in different situations. Signage companies use them for outdoor signs that can stay vibrant even in bad weather. Labels on things like food packaging and cosmetics also use these inks because they last a long time and don’t fade easily.
Pros and Cons of UV-Cured Inks
Pros
- Instantaneous drying: Eliminates waiting time for handling printed materials.
- High print quality: Produces sharp images with vibrant colors.
- Versatile application: Suitable for various substrates, including plastics, glass, and metal. Additionally, our aqueous coatings are compatible with silicone, making them ideal for use with silicone-based printing inks in screen printing applications.
- Enhanced durability: Resistant to scratching, fading, and chemicals.
- Environmentally friendly: UV-cured inks, commonly used in screen printing, are typically solvent-free and emit fewer volatile organic compounds (VOCs). These inks are often applied with aqueous coatings, which can include silicone additives for enhanced performance.
Cons
- Limited flexibility: UV-cured inks may not be as flexible as heat-set inks on certain screen printing materials due to the nature of silicone coatings and water content.
- Higher cost: The initial investment for UV printing equipment, including coatings and silicone screens, can be more expensive compared to traditional water-based methods.
Ready to Get Custom Packaging for Your Business?
start with a low minimum order quantity
Comparison Between Heat-set and UV-cured Ink
Heat-set and UV-cured inks are both commonly used as water-based ink solvents in the printing industry, particularly in commercial printing and packaging applications, but they differ from water-based inks and solvent inks in some key aspects. In this blog, we’ll provide a brief overview of the differences between the two types of ink and explain why they’re both valuable in different situations.
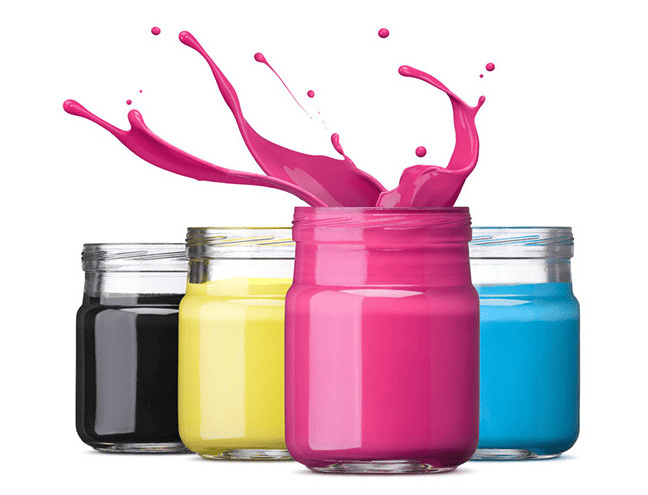
1. Drying Methods
Heat-set ink relies on the application of heat to dry and set the screen printing ink on the substrate, curing properly, while fully cured and UV-cured ink utilize a light curing process. The screen printing coatings used in heat-set ink and fully cured ink are water-based or aqueous.
2. Impact on Production Speed
UV-cured ink offers a significant advantage over dried ink films in terms of production speed in screen printing. Its rapid drying time eliminates all the prints that need extended drying periods for dried ink film, allowing for faster turnaround times for all these prints. This is possible because UV-cured ink utilizes coatings that are water-based or aqueous.
3. Print Quality Comparison
Both heat-set and UV-cured inks produce vibrant colors in screen printing. However, they differ in their finishes. Heat-set ink typically results in water-based or reactive inks with a glossy finish due to good chemical resistance of the coatings used, while UV-cured ink can achieve a matte appearance with the help of aqueous deposition.
4. Environmental Considerations
There is a notable difference between heat-set and UV-cured inks in the dry touch screen printing process. Heat-setting processes can emit volatile organic compounds (VOCs), which have negative environmental impacts. On the other hand, UV-curing ink technology uses low VOCs, making it more environmentally friendly for aqueous coatings.
Factors to Consider When Choosing: Heat-set Inks or UV-cured Inks
Selecting the right ink is crucial for achieving optimal results in screen printing. Two popular options for solvent inks on the market are heat-set ink and UV-cured ink. Each type has its own unique characteristics and advantages that make it suitable for specific printing requirements.
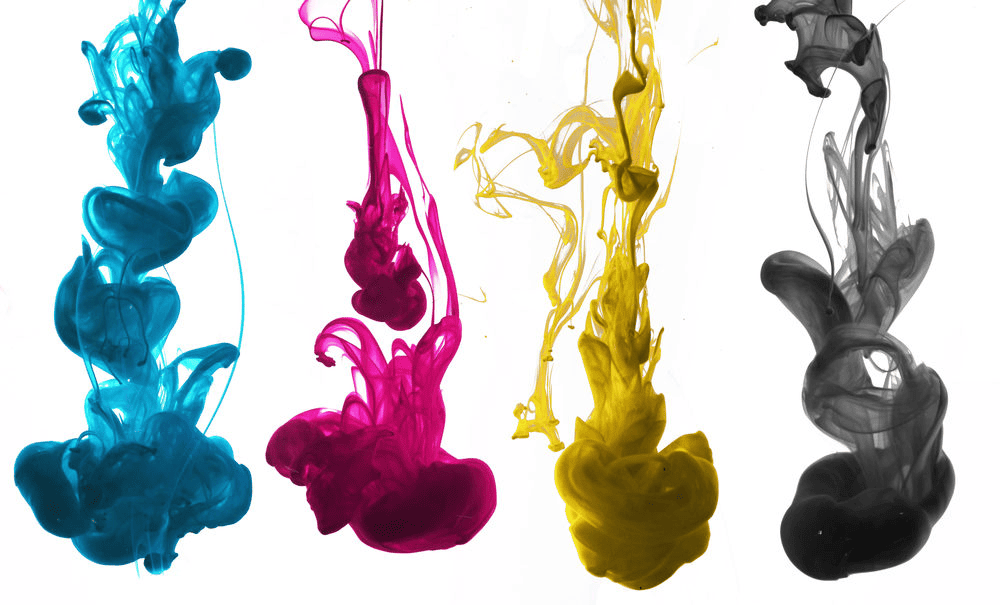
1. Printing requirements
The nature of the printing process in your print job plays a significant role in curing ink and determining which curing stage of ink is best suited for your needs. Heat-set inks are commonly used as initially cured inks for high-speed commercial printing processes, such as web offset or rotogravure printing. On the other hand, UV-cured inks are ideal for applications that require instant drying, such as screen printing or digital printing.
2. Cost implications
Cost is an important consideration when deciding on the type of ink to use. Heat-set inks typically have lower upfront costs but may require additional energy consumption during the initial drying and curing process. UV-cured inks, while initially more expensive, offer faster curing times and reduced waste due to their instant drying and complete curing properties.
Ready to Get Custom Packaging for Your Business?
start with a low minimum order quantity
3. Compatibility with substrates
Different substrates may have varying compatibilities with heat-set and UV-cured inks. Heat-set inks work well on absorbent materials like paper or cardboard, whereas UV-cured inks can be used on a wider range of substrates, including plastics, glass, metal, and even textiles.
4. Availability
The availability of both types of ink should also be considered based on all these factors, including your location and supplier network. Heat-set inks are widely available and commonly used by ink manufacturers in many printers globally. However, UV-cured inks have gained popularity due to advancements in technology and increased demand for environmentally friendly alternatives.
Start Your Printing with Packoi Printing
In conclusion, whether you choose a thermosetting ink or a UV-curable ink depends on your specific printing needs. Any ink can be an ideal choice, depending on your needs.
Packoi Printing is here to meet your different needs. We have a wealth of printing experience, and high-quality printing processes and finished products.
Packoi Printing can help you print your advertising, brochures, posters, product catalogs, and other marketing materials more easily and conveniently.
Contact us today to start your printing!